- Local time
- 10:47 AM
- Joined
- Apr 13, 2012
- Messages
- 39,714
- Reaction score
- 146,506
- Location
- Granite Bay CA
I'm doing a cam swap in the 440/493 in the Charger. This will include changing the valvesprings. I wanted a PowerMaster valve spring compressor, but Summit didn't expect to have them for 2 weeks. I figured I'd try to make my own.
I made the loop narrow enough for this to work on both big blocks and small. Please forgive the sloppy welds!
Materials cost: About $5. The Powermaster tool is over $100. SCORE!
- - - Updated - - -
I wanted to give the tool a high visibilty color. It didn't occur to me that it turned out Harbor Freight orange...
Uuuuugh!
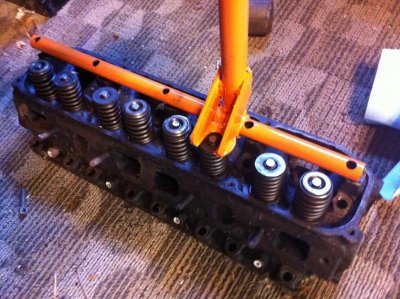
I made the loop narrow enough for this to work on both big blocks and small. Please forgive the sloppy welds!
Materials cost: About $5. The Powermaster tool is over $100. SCORE!
- - - Updated - - -
I wanted to give the tool a high visibilty color. It didn't occur to me that it turned out Harbor Freight orange...
Uuuuugh!
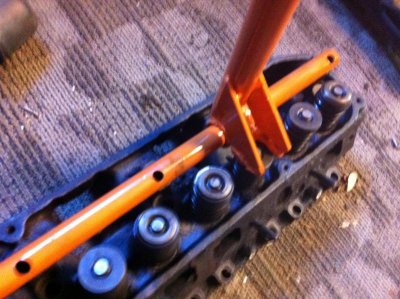
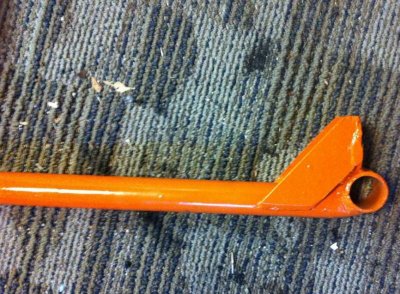
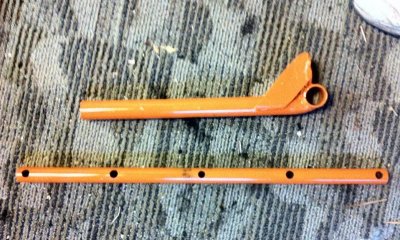
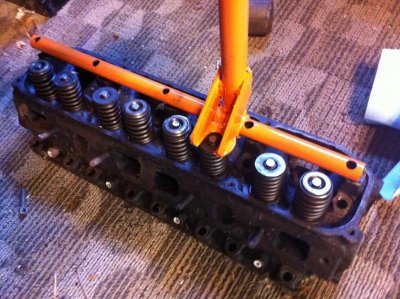