I need to know if any adjustable or expandable reamer would be worth trying.
Long story short.
I made fixture and using the flywheel for a guide I drilled out this 383 forged crank for the 833 input shaft in situ since the engine didn't need anything else.
I have done this on cast cranks/cut shafts before and used a register bearing. (Glyptal or red varnish. No leaks so far)
Yes, the forged crank fought me.
The engine had an INCORRECT bushing in it. So that is what is in the picture. (Don't ask)
But I was NOT going to cut this new input shaft.
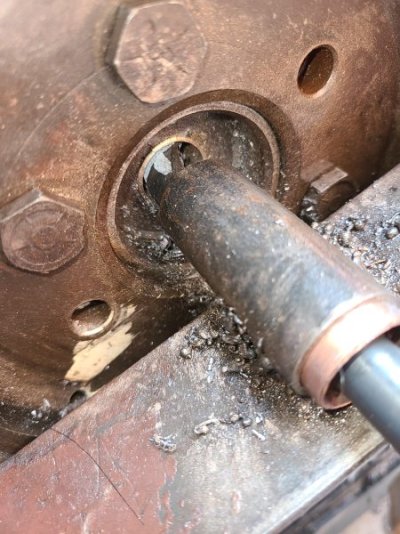
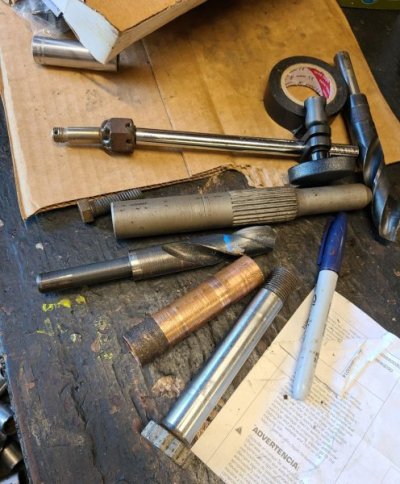
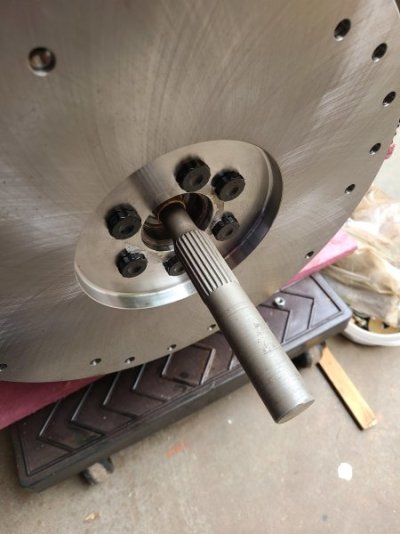
I found out that the AMERICAN bearing Brewers sells CAN be removed with this puller.
So will a bushing. Whoever designed this should get Noble prize.
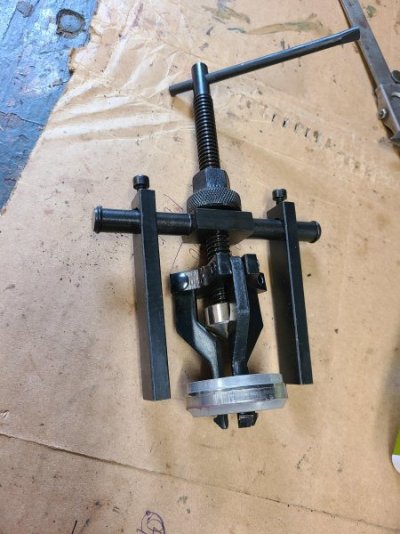
This is what I have and my question:
Will either an adjustable OR expandable reamer work?
I don't mind giving it a try if it's possible (What to buy?)
I turned down a .940 bushing to .890 and it was a press fit so I'm pretty sure .885 is accurate.
Crank pilot bushing part#/size needed?
Post 8 there.
The reduced bushing only went in 3/8 inches which is too short and too thin for comfort.
It's not a space ship or airplane so close is good enough for me.
Might be a little off on total the depth given the drill point.
The clearance on the shaft is good though with the trans installed.
Some related info for reference.
With .021 offsets this is as close as I'm going to get it.
I give up.
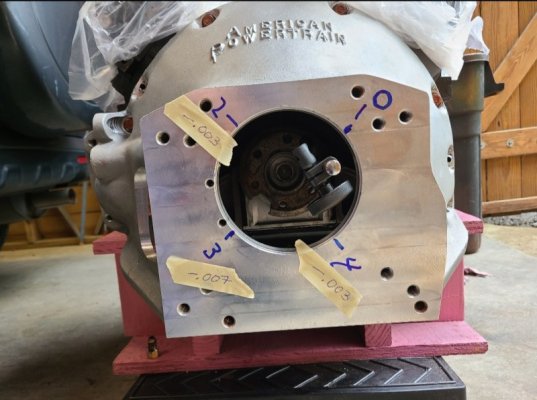
I bought the new housing during the lock down. Just grabbing things.
I have the original bell and engine but this is a completely new drivetrain.
APT didn't even have any. Found APT aluminum one at Summit.
It came with to adaptors . One was undersize the other was oversize sloppy.
Had to call APT last month and have them look through a pile to buy the correct size since everyone is so into this runout thing now. (Yes.)
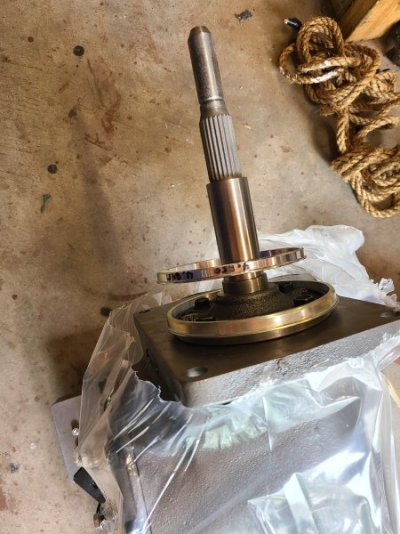
Check the starter clearance.
It had two milling cuts and I had to clean our extra material between them.
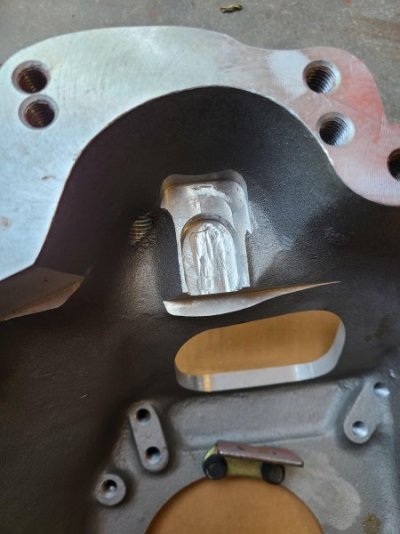
No body makes a boot for this animal.
But this Chrysler one works just perfect if you cut off the inner lip and use 8/X32 machine screws.
Leave the middle material.
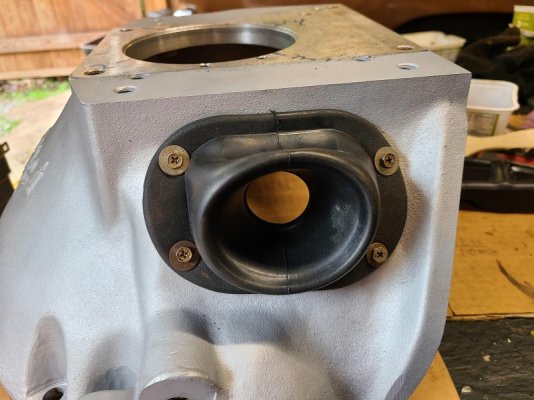
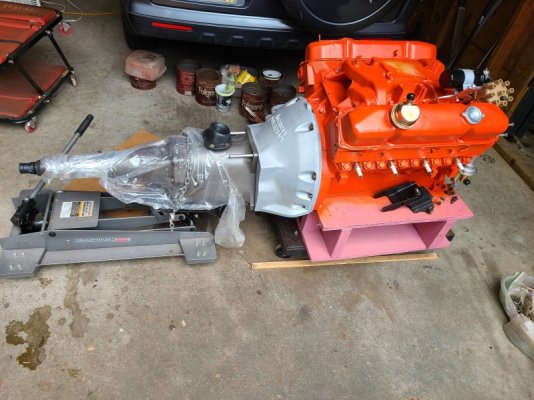
Long story short.
I made fixture and using the flywheel for a guide I drilled out this 383 forged crank for the 833 input shaft in situ since the engine didn't need anything else.
I have done this on cast cranks/cut shafts before and used a register bearing. (Glyptal or red varnish. No leaks so far)
Yes, the forged crank fought me.
The engine had an INCORRECT bushing in it. So that is what is in the picture. (Don't ask)
But I was NOT going to cut this new input shaft.
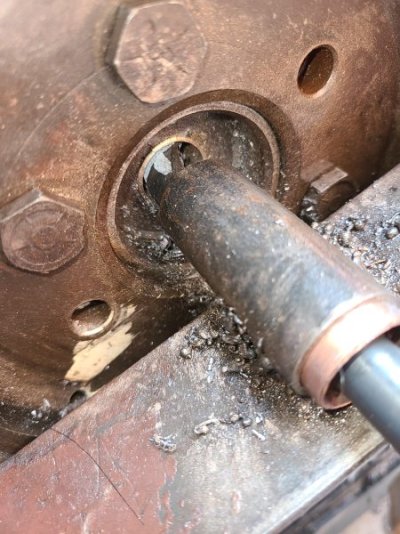
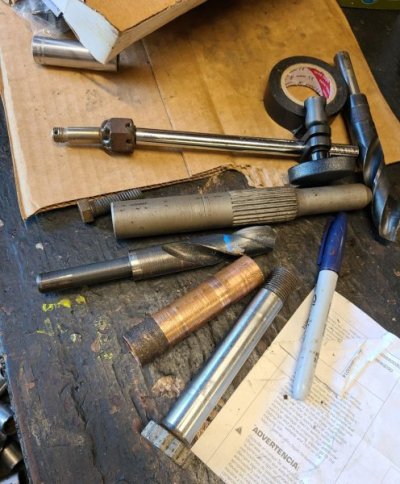
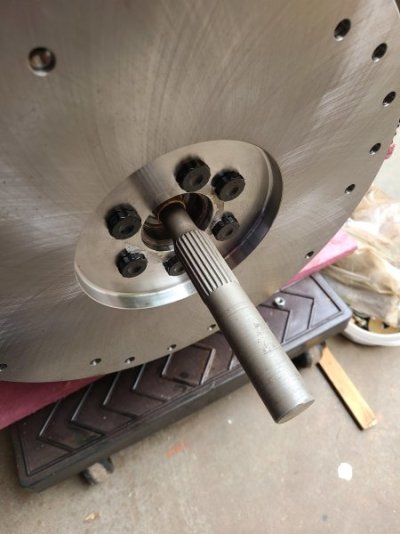
I found out that the AMERICAN bearing Brewers sells CAN be removed with this puller.
So will a bushing. Whoever designed this should get Noble prize.
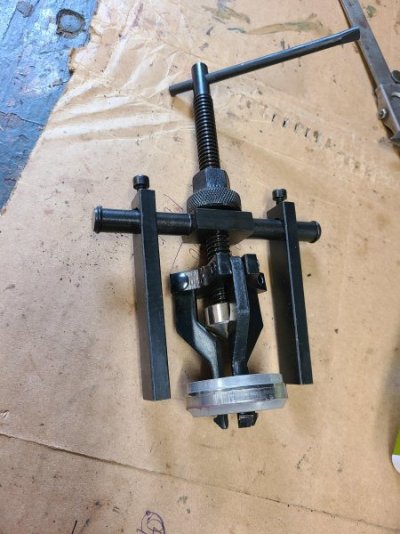
This is what I have and my question:
Will either an adjustable OR expandable reamer work?
I don't mind giving it a try if it's possible (What to buy?)
I turned down a .940 bushing to .890 and it was a press fit so I'm pretty sure .885 is accurate.
Crank pilot bushing part#/size needed?
Post 8 there.
The reduced bushing only went in 3/8 inches which is too short and too thin for comfort.
It's not a space ship or airplane so close is good enough for me.
Might be a little off on total the depth given the drill point.
The clearance on the shaft is good though with the trans installed.
Some related info for reference.
With .021 offsets this is as close as I'm going to get it.
I give up.
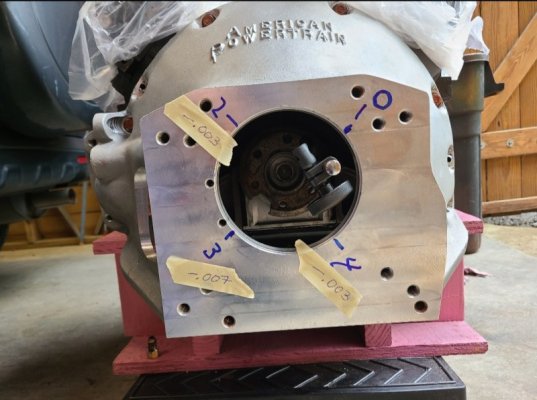
I bought the new housing during the lock down. Just grabbing things.
I have the original bell and engine but this is a completely new drivetrain.
APT didn't even have any. Found APT aluminum one at Summit.
It came with to adaptors . One was undersize the other was oversize sloppy.
Had to call APT last month and have them look through a pile to buy the correct size since everyone is so into this runout thing now. (Yes.)
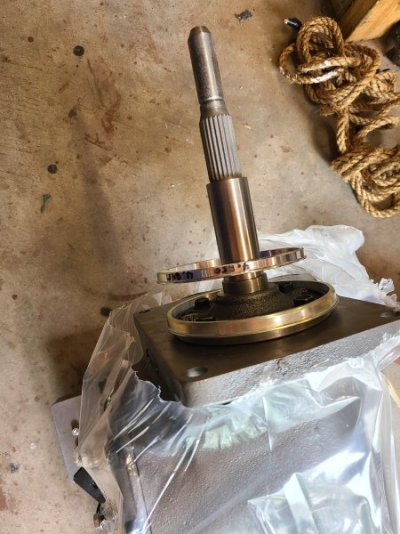
Check the starter clearance.
It had two milling cuts and I had to clean our extra material between them.
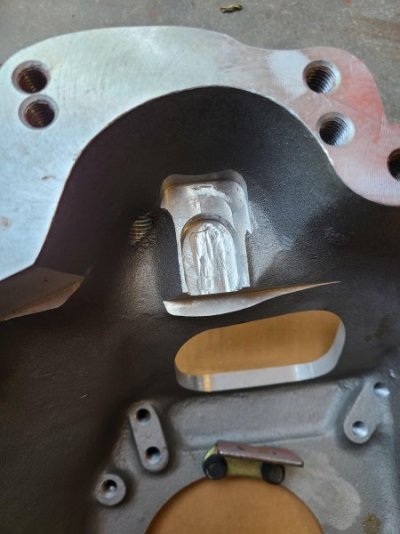
No body makes a boot for this animal.
But this Chrysler one works just perfect if you cut off the inner lip and use 8/X32 machine screws.
Leave the middle material.
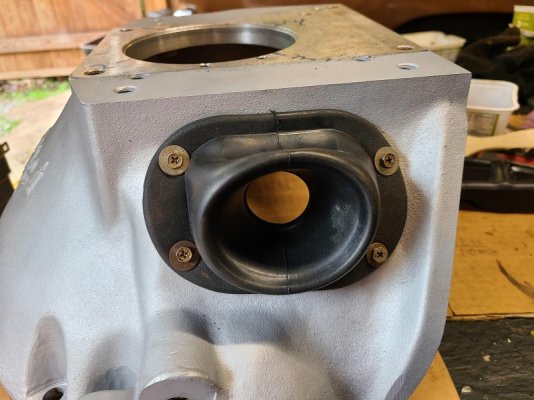
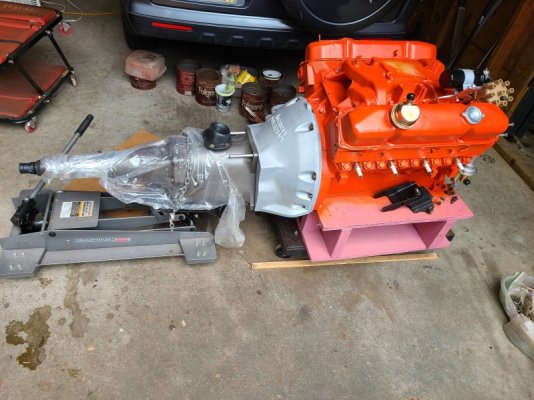
Last edited: