morrow_jacob
Well-Known Member
I bought a 1970 B body Dana 60 for my 68 Charger, and I have sold my 8 3/4 (to be delivered next week). The Dana 60 had the perches moved for its application and now I need them back in the stock location.
The best way I can figure to get them back in the right spot, was to put the original axle level at its perches and then measure the pinion angle with the flat part of the pinion up and my angle finder on top. It looks as though its right at 7 degrees. Then I'm going to put the dana at 7 degrees and level the new perches and put them at 44''.....
Does this sound like the right way to go? I've never moved perches before....
Also, I am more experienced with my mig than my tig, should I still give it a try with my tig? 115v mig 220v tig btw
Thanks in advance.
(I dont know how to get rid of the attached image)
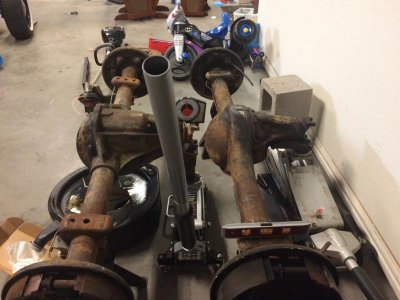
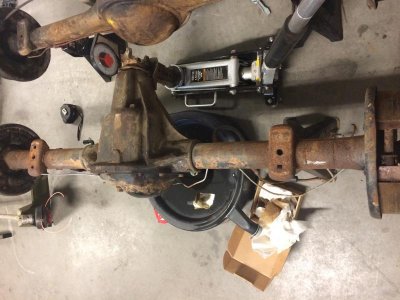
The best way I can figure to get them back in the right spot, was to put the original axle level at its perches and then measure the pinion angle with the flat part of the pinion up and my angle finder on top. It looks as though its right at 7 degrees. Then I'm going to put the dana at 7 degrees and level the new perches and put them at 44''.....
Does this sound like the right way to go? I've never moved perches before....
Also, I am more experienced with my mig than my tig, should I still give it a try with my tig? 115v mig 220v tig btw
Thanks in advance.
(I dont know how to get rid of the attached image)
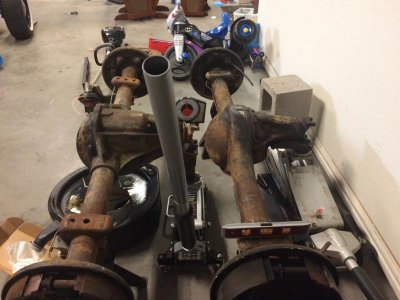
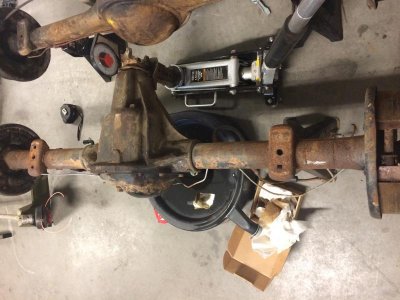