bandit
Well-Known Member
I am in the process of prepping the body for painting and working on the cowel right now. Right at the edge on both sides where it meets with the corner of the windshield, I had some ugly cracks. They looked like a bad bondo job that was starting to crack but after grinding one side down, I see it is lead filler and it came out quite easily because rust started under it. They apparently used the lead to help round the corner. What do you guys use to fill deeper gouges like this? I have no skills in leading so would like other alternatives and think this would stretch the bounds of body filler. I would say about 1/4 inch needs to be filled back in. (and I need to kill that rust that leaked in under the lead too)
Does using some JB Weld sound crazy??
Here are some pics.
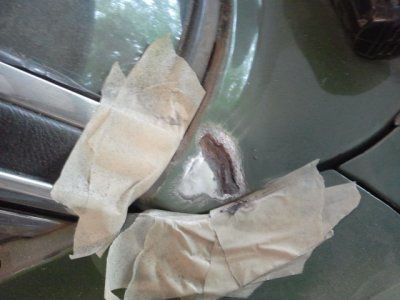
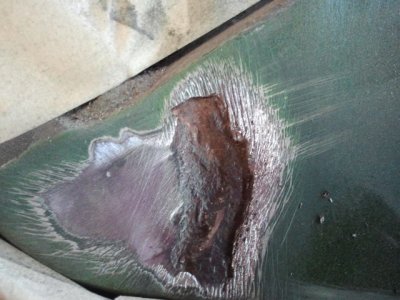
Does using some JB Weld sound crazy??
Here are some pics.
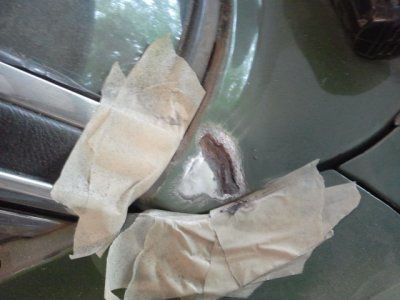
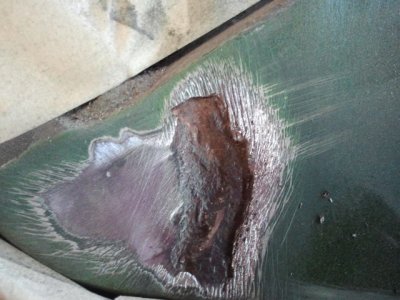