For now, 4.5 is fine. At first it was set at about 1 psi and the engine wouldn't idle. I winged it until it would idle, at about 2.5 psi, then at idle I set the regulator at about 4.5. I have no intention of driving the car aggressively, or even off my block until I get a better pump, probably an Edelbrock. 6 psi would be on the cusp of overwhelming the needle valves.4.5 psi is a bit low, will give low fuel level; about 6 is better.
Currently I'm using a 1966 washer bottle with the hose bib as a fuel tank. Idling for about 8 minutes dropped the fuel level about a half inch. I need to calculate the fuel use after I figure out how much fuel that actually was. The engine idles well for not running for such a long time. But it's been parked in weather-tight garages since I've owned it, 40 years now, so I wasn't expecting any issues. I was sure to prepare it by hand-rotating the engine with fresh oil in the cylinders, cleaned and re-gapped plugs, cleaned points, etc. Still, it needs a complete tune up with new plugs, wires, and points. Those have all been in the car since I bought it in the 1980s.
I have a rust hole on the torsion bar support I need to fix before I run the new fuel line. I also haven't installed the new tank yet, I wanted to wait until the engine was running again. I figure by next spring I'll get the tank in and the car off the jack stands and finally out of the garage.
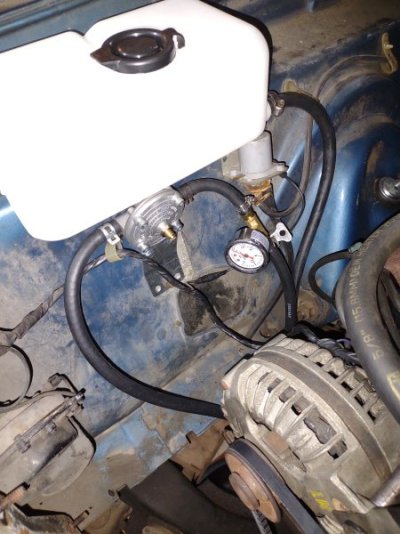