- Local time
- 4:59 PM
- Joined
- Oct 16, 2014
- Messages
- 29,607
- Reaction score
- 73,175
- Location
- Salisbury, Vermont
Hey folks. Ghost here. I have a problem with which I need help, and or, guidance.
The quarter tail extensions on the Express ( 67 Coronet) have been modified to accept the 66 Thunderbird tail lights. However, so far, every method of bonding the new "U" channel to the pot metal extension body has failed. I have tried, so far, two part epoxy, panel bond, and expanding foam as a filler. I need this to work so I can finish the bodywork.. I'm now thinking that I need to "make" this extension out of something else besides pot metal. Like fiberglass, acrylic, plastic, aluminum or SOMETHING! Any suggestions and ideas, however wild, are cool as long as they are meant to a constructive solution of sorts. Frustration is clouding my thought process and I'm out of ideas.
Basically, I sliced the stock "U" shaped cavity, in which the stock tail lights sit, away from the outer body of the extension. This leaves the extension shell to which I need to apply the new "U" channel which is wider, top to bottom and more pointed in a "VEE" than a "U" at the outer ends. Nothing seems to stick the two pieces permanently together, the pieces being pot metal and sheet metal. Discuss please......thanks.
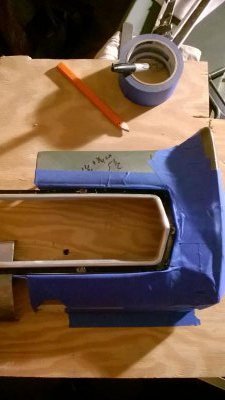
The quarter tail extensions on the Express ( 67 Coronet) have been modified to accept the 66 Thunderbird tail lights. However, so far, every method of bonding the new "U" channel to the pot metal extension body has failed. I have tried, so far, two part epoxy, panel bond, and expanding foam as a filler. I need this to work so I can finish the bodywork.. I'm now thinking that I need to "make" this extension out of something else besides pot metal. Like fiberglass, acrylic, plastic, aluminum or SOMETHING! Any suggestions and ideas, however wild, are cool as long as they are meant to a constructive solution of sorts. Frustration is clouding my thought process and I'm out of ideas.
Basically, I sliced the stock "U" shaped cavity, in which the stock tail lights sit, away from the outer body of the extension. This leaves the extension shell to which I need to apply the new "U" channel which is wider, top to bottom and more pointed in a "VEE" than a "U" at the outer ends. Nothing seems to stick the two pieces permanently together, the pieces being pot metal and sheet metal. Discuss please......thanks.
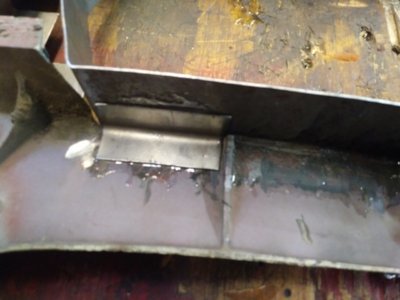
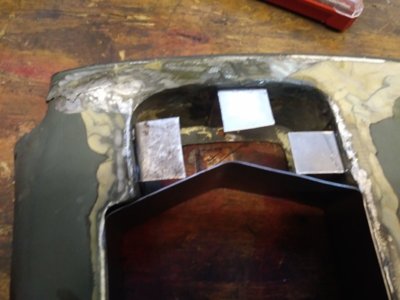
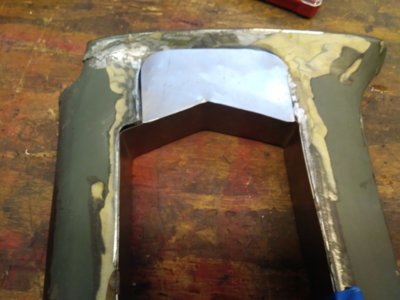
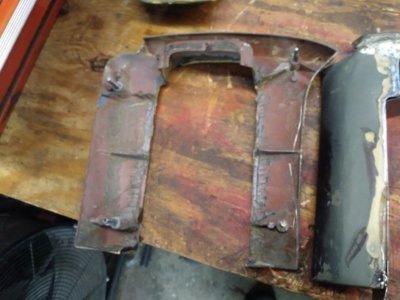

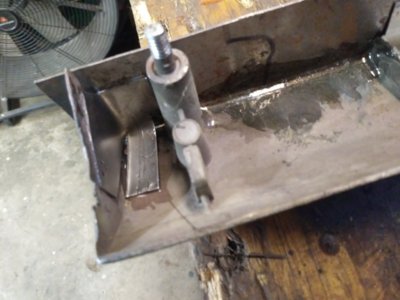
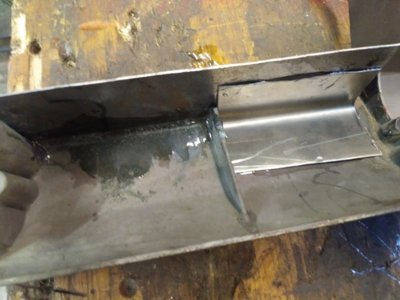
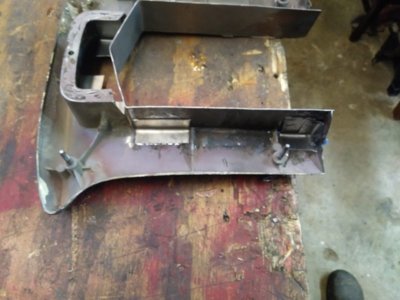
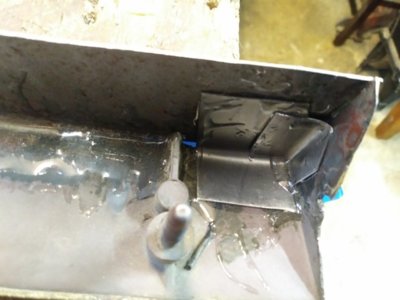
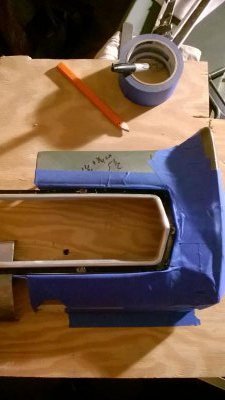