Wietse
Well-Known Member
Hey guys,
In my '69 Coronet R/T i have a 440, which has been rebuild in the past but i have no specs about it.
The engine has a bit rough idle and low vacuum (10Hg) so i want to find out what camshaft specs it has in there.
By knowing the specs i might not find the exact part number (who knows it is a one-off grind) but i can hopefully determine the effective rpm range of this camshaft by comparing it with other camshafts with similar specs.
Current converter specs are also unknown, (someone advised met to do a check on the flash stall to get a close idea of the stall speed)
As i want to change my 4.10 ratio rear axle to a 3.23 or 3.55 ratio so i will have to consider all this to get a decent match for drivability. (cam, converter, rear axle ratio)
So, to do this i ordered a degree wheel and got a magnetic stand with digital dial gauge.
I know i have flat tappets, most likely hydraulic ones as i can see a circlip inside on de pushrod end. (maybe not, but hoping you guys know why the circlip is there, see pic)
There is no valve lash at all at any time, the push rods can be turned by fingers when the tappet is on the base line of the cam. (not loose, you need to apply a little force to rotate them)
I want to clear these things up first:
* Can i use the dial gauge and take the measurements on top of the rocker arm, right next to the adjustment screw of the push rod and confirm degree's and lift?
(setting it up in such a way that it is inline with the angle of the pushrod and in center of the adjustment screw)
* If they are hydraulic tappets, will they not cause a false reading when checking due to oil loss or so when they fight against the valve spring?
I am not sure about the rocker arm ratio (think 1.6) so to avoid a false reading due to incorrect ratio correction i want to avoid measuring on the valve spring retainer.
I don't want to pull any parts out because with my luck i am bound to **** something up, and there is no need for pulling parts out of this working engine.
Regarding the camshaft, the only ID i found on the camshaft is CWC.
I traced it back and found this is Campbell, Wyant & Cannon, located in Muskegon, Michigan and they don't exist anymore under that name, now called Kautex, a Textron company.
And they manufacturer camshaft casts.
The do not do any grinding, just make the raw casts and sell them to the manufacturers who grind them to their own specs and sell them to the public.
It might be this is a one off grind done by a machinist who made a specific camshaft for a client, it could be as well that a company like Comp Cams or any other camshaft manufacturer use these as well, no idea.
Any thoughts and suggestions are welcome as always!!
Thx for reading!!
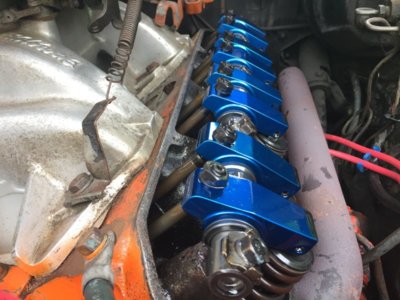
In my '69 Coronet R/T i have a 440, which has been rebuild in the past but i have no specs about it.
The engine has a bit rough idle and low vacuum (10Hg) so i want to find out what camshaft specs it has in there.
By knowing the specs i might not find the exact part number (who knows it is a one-off grind) but i can hopefully determine the effective rpm range of this camshaft by comparing it with other camshafts with similar specs.
Current converter specs are also unknown, (someone advised met to do a check on the flash stall to get a close idea of the stall speed)
As i want to change my 4.10 ratio rear axle to a 3.23 or 3.55 ratio so i will have to consider all this to get a decent match for drivability. (cam, converter, rear axle ratio)
So, to do this i ordered a degree wheel and got a magnetic stand with digital dial gauge.
I know i have flat tappets, most likely hydraulic ones as i can see a circlip inside on de pushrod end. (maybe not, but hoping you guys know why the circlip is there, see pic)
There is no valve lash at all at any time, the push rods can be turned by fingers when the tappet is on the base line of the cam. (not loose, you need to apply a little force to rotate them)
I want to clear these things up first:
* Can i use the dial gauge and take the measurements on top of the rocker arm, right next to the adjustment screw of the push rod and confirm degree's and lift?
(setting it up in such a way that it is inline with the angle of the pushrod and in center of the adjustment screw)
* If they are hydraulic tappets, will they not cause a false reading when checking due to oil loss or so when they fight against the valve spring?
I am not sure about the rocker arm ratio (think 1.6) so to avoid a false reading due to incorrect ratio correction i want to avoid measuring on the valve spring retainer.
I don't want to pull any parts out because with my luck i am bound to **** something up, and there is no need for pulling parts out of this working engine.
Regarding the camshaft, the only ID i found on the camshaft is CWC.
I traced it back and found this is Campbell, Wyant & Cannon, located in Muskegon, Michigan and they don't exist anymore under that name, now called Kautex, a Textron company.
And they manufacturer camshaft casts.
The do not do any grinding, just make the raw casts and sell them to the manufacturers who grind them to their own specs and sell them to the public.
It might be this is a one off grind done by a machinist who made a specific camshaft for a client, it could be as well that a company like Comp Cams or any other camshaft manufacturer use these as well, no idea.
Any thoughts and suggestions are welcome as always!!
Thx for reading!!
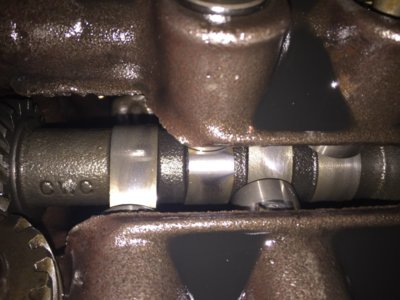
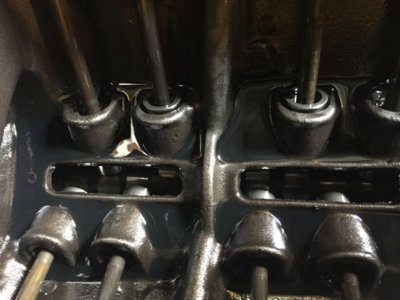
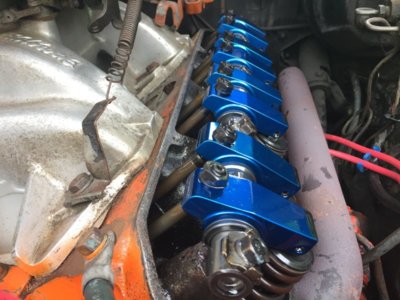