Based on other members observations and input, I pulled my head out of my butt and got the Watts link straightened out. Thanks again for the heads up!
The mounts are not completely welded in but they're certainly not going anywhere.
Next is going to be work on the exhaust then back to the rear shock mounts: the factory location I'm currently using might not have enough clearance but I won't know until I get some other parts and start moving things up and down.
I'm having all kinds of difficulty with the welding even after changing over to a Lincoln 200 MIG (plenty of power!!!)
For instance:
1) I'm seeing great penetration in the base metal but I'm getting far too much weld material on the weld itself. I've tried slowing down the wire speed but then I don't seem to get the consistent penetration
2) I grind everything I'm going to weld so there's no contaminants, yet I'm getting a great deal of popping and sputtering; I've got the gas pressure at a touch over 30 and am considering going a bit higher but don't want to be pissing gas pointlessly
I'm curious if the replaceable tip is too far inside the cup, leaving too much distance between the tip and the material being welded? I've watched some instructional vids and know how critical this distance is.
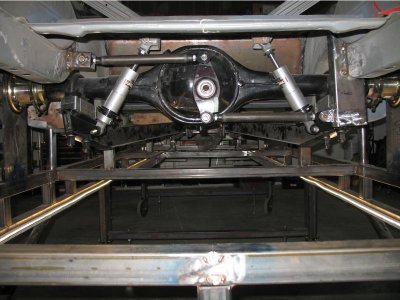
- - - Updated - - -
I have GOT to start playing that Power-Ball because all this work and real-life stuff keeps getting in the way of my working on the Fury! Over the past few weeks I've had precious little time to devote to the car but I was able to notch the rear frame rails and then spent my entire Father's Day weekend working on the Fury and finished off one of the most crucial elements; the transmission cross-member. Now that the cross-member is finished we can finalize the exhaust routing, then drop in a floor, build the trans tunnel (that'll come much later) and build the firewall. Oh yeah, my ability to weld seems to have miraculously returned now that I re-did the ground strap! Not that I'm some kind of artisan or anything but my welds are MUCH better than before! Here are some pix and updates:
While the 9" rear axle tubes didn't actual contact the frame rails, they were way too close for my comfort so I notched the rails 1". I simply cut vertically on the front and rear of the rail then joined the cuts with a horizontal cut, removed 1" from the top of the piece I just removed, then welded it back into the frame rail. I filled the gaps with 1/8" plate to ensure the strength, and while the rail lacks the perfectly rounded appearance of the original I can live with the results:
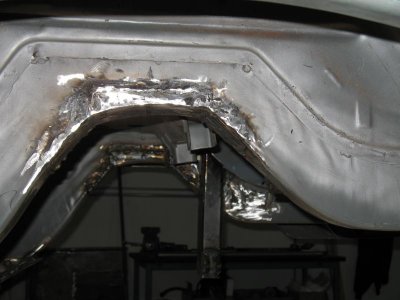
After finishing off the frame rail notches I got to work on the cross-member, which is very similar in concept to the cross-member of my '70 Vette; the exhaust tubing passes directly through the cross-member as opposed to bending or contouring the cross-member around the exhaust. Here is how I did it:
I don't have a TIG welder nor the talent to use one, so before anything else happens I need to take my stainless exhaust pieces and have some flanges TIGged in place, then we'll finalize the exhaust and move on to the other areas I mentioned above. It'll probably be a couple weeks minimum before I can do much more work; family and work call me again!
- - - Updated - - -
Moving to a new area means building new relationships and finding quality craftsman, and luckily I've found a guy who knows how to wield a TIG torch; his name is Adam and he's co-owner of a prop-repair shop in Henderson. Over the past week Adam welded on the stainless flanges and flex-joints of the 3" exhaust which if all goes well I'll be getting mocked into place this weekend.
- - - Updated - - -
Passing the exhaust through the frame-rail seemed like a good solution to a problem I caused myself (running Truck-arm rear suspension) but damn it's been a ton of work to make functional, including the exhaust.
Since the exhaust passes through the frame rails at 45 degree angles and the tubing itself has bends and flanges attached, sliding the tubing through the rails became a frustrating repetition of making the holes larger and larger until I could snake the tubing through, and in the end all that cutting left me with oblong holes in the frame that were MUCH larger than the 3" exhaust passing through. Knowing the exhaust tubing (stainless) would be an integral part of the frame (for strength) meant I couldn't have huge gaps around the tubing so I spent literally hour after hour fabricating little crescent shaped patches out of extra frame rail material. Each crescent was unique so making a single pattern was useless, hence each one of the 4 was rough cut out with the Plasma cutter then meticulously ground and filed to fit. Below are some shots of the crescents and the overall exhaust layout:
These two shots are the crescent patches (outside of frame rails) tacked in place. I am going to use a different method to patch the holes on the inside of the frame rails and want to wait until I have those patches done before final welding everything.
I can't even remember when I bought the stainless Borla mufflers but having seen bunch of Sprint cars running Spintech mufflers I thought they'd be worth a look. Why? The Borla's are 4 1/2" thick, which was as thin a muffler as I could find with 3" inlet/outlets, and even at only 4 1/2" the thickness will force the muffler to hang slightly below the bottom of the frame rail and protrude slightly into the floor pan. The Spintech 6000 series turn out to be only 4" thick so you know I had to go ahead and order those, right? Yep, so anyone looking for a brand new set of polished stainless Borla mufflers let me know
Here's what Spintech's look like:
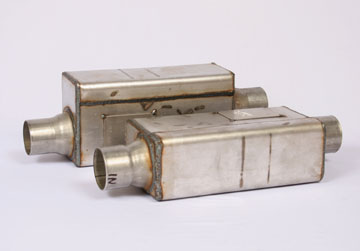
- - - Updated - - -
My free time to work on the Fury has been a bit limited lately but I have been making some solid progress. Without having a mill or lather at your disposal sure slows things down, but with some patience and sweat I finally finished the frame reinforcements that surround the exhaust tubing. Where the reinforcements meet the frame I've used standard MIG welding but for welding the reinforcements to the stainless exhaust I'll need to pick up some "Tri-Gas" and stainless wire; I figure to do that this week if time permits.
Here are a few shots of the progress I've made over the past couple weekends, and one thing I'm really happy about is the fact the new Spintech mufflers are slim enough they do not hang below the level of the frame. Granted, the turn-downs do but I can live with that so long as the mufflers don't.
- - - Updated - - -
Progress has been slow but steady over the past few weeks and either I'm punch-drunk or there really is some light at the end of the tunnel! If you've read through the entire post you saw the floors had already been mocked up but dealing with the driveshaft/trans tunnel was a completely separate process, so that's what I've been focusing on lately.
To get the tunnel started I put the rear suspension back in the car, and using a measured drawing located the centerline of the pinion (I don't have a carrier yet) and shot a line from the centerpoint up to the trans yoke. Knowing where the shaft would run was the easy part but I had to remember the parking brake will be fitted to the pinion as well so I needed to ensure there was enough room, both horizontally and vertically, for the caliper and rotor to fit. Once I had the measurements dialed in I cut the far rear of the floorpan in an arc and welded a flange around the perimeter.
I have the tunnel completed and ready to go in, but like a dunce I forgot to take a picture. I'll snap one soon and show you the finished look. I'm waiting on new arms for my spot-welder, and as soon as they arrive I'm going to start putting the floors in permanently...I can't wait!
- - - Updated - - -
I swear it feels like everything in the world is conspiring to keep me from working on the Fury! $5K worth of electrical to build my shop, two broken arms last Christmas, surgery 3 weeks ago to repair damage when I broke my wrist, when does it end? Enough pissing and moaning, I've FINALLY begun putting the floor pans permanently in the car! I can't wait to get this done but for now I'm just about halfway so here are some pix:
I chose to put a rosette weld about every 2 inches or so, which combined with the heavier gauge steel I used makes for one sturdy floor! Glad I'm using fiberglass for all the body panels because with the AM chassis and all the steel I'm using I'll need to cut some weight!
One thing I have consistently seen; "Weld-through Primer" makes for one messy, splatter-filled weld! It's been so long since we did the wheel tubs I'd forgotten how terrible that primer is to weld through, but did I ever get a shocking reminder! Granted, it's better than not priming the surfaces at all but it does make for some icky welds and lots of clogging the tip of the gun.
Oh well, lunch is done so now it's on to the driver side.
- - - Updated - - -
Holy sh*#, it's been 6 years since I began this build, which says I'm either REALLY slow or REALLY persistent; I hope it's persistent! I mention this because I reached a milestone today, the floor of the Fury is actually in! I can't believe it but yep, it's in and secure. Next I'll get the back half of the tunnel in then get moving on the firewall and cowl, but for now I'm going to savor the moment. Here are some shots:
- - - Updated - - -
Not a lot of time to work today but I got the rear half of the tunnel welded into place.
I don't know if I EVER remember having so much weld splatter as what I experienced putting in the floors and tunnel. No matter how much I ground and wire-brushed the surfaces it's as if the weld would pop/splatter/explode and leave a divot in the puddle, all of which was surrounded by a black soot. More power, less power, more wire speed, less wire speed, nothing seemed to change the phenomenon. I have to figure this out so any ideas would be most welcome.
Here's the tunnel:
- - - Updated - - -
Today marked a milestone of sorts; the floor and tunnel are now complete all the way up to the firewall! Who'd have thought a trans tunnel would be so much work, but with all the various angles, elevation changes, etc, this thing was WAY more difficult than I ever would have imagined. I guess I could have used thinner steel than the 16 gauge I've been using throughout the build, but I like the strength and solidity it adds.
Here are a couple shots of the tunnel in place, and you can see how difficult it was to meld the factory tunnel/hump into the finished tunnel. BTW - sorry about the blurry shots, I guess I'm neither a welder OR a photographer!
One thing I did find out via some experimentation before installing the front half of the tunnel today; I slowed down the feed speed on the welder well below the recommended setting and found my weld penetration to be better as well as less popping and f'ing up. Still not perfect but certainly better, so maybe I'll switch to .030 instead of the .035 I've been using. Just a thought.
- - - Updated - - -
I've now tried .023 at settings and wire speeds from high to low, with every combination in between; no real luck.
I've gone back to .030 while trying every combination I can think of; no real luck.
I've raised and lowered the gas flow rate; no real luck.
The welding results come out to a far lower standard than I have been able to produce in the past, so now I'm left to wonder if:
a) I've got some kind of degenerative disease that's eroded my skills and left me unable to figure out simple problems
b) the bottle of gas I've been using (almost empty) may have an incorrect mixture
c) go back to "a"
Is there anyone with welding skills located in Las Vegas that'd be willing to come to my shop and try to diagnose WTF is wrong? I could really use the help!
- - - Updated - - -
The original cowl turned out to be just too far gone; I couldn't see continually fighting with it to make it work, so I got hold of DVAS and purchased a complete cowl/firewall. Granted, when the part arrived it turned out to be from a '65 as opposed to a '64 but save for some small/minor differences the replacement is identical to the original, and since this is anything but a concourse restoration I'm completely devoid of any concern.
Here's the replacement piece. If you're a real Mopar fiend you'll notice the shape of the hole for the steering column and some differences around the heater/airbox area, but the overall shape of the window frame, door frame, cowl, etc. are all the exactly the same.
Before I cut the original sheet metal away I made some alignment jigs that mount to the chassis plate; they're removable but are self-aligning so I can take them off and put them on with ease and they're always in the same exact location. In the second picture you'll see a vertical 1" x 1" bar, the upper edge lining up with the factory seam where the door jam meets the A-pillar; what a perfect point this turned out to be in terms of lining up the replacement!
I also added some vertical, horizontal, and diagonal bracing to the cowl area inside the car, using mounting locations provided by the factory, that way I could make the replacement cowl line up accurately to the same position as the original: