Door Panels
While the original material was a coarse loose orange fiber I opted for a sheet of thin polyester batting typically used for little old ladies making quilts. Sorry for the potato quality pictures, I really need to stop using my camera phone. Looks great on that little screen until I load them up to the laptop!
First thing I did was install the door panel clips (thanks fk5bird!), positioning them to match the passenger side. Then using the batting laid it down for an idea of where it needed to go, cut it then used a spray adhesive (believe it was 3M super 77) to stick it together. Do want to keep it stretched so it's even across the entire surface.
After it had dried a bit went back and trimmed up all the excess.
Wish I had taken more pictures of this part but was a bit of a hands on ordeal so will walk through how I did it.
Using DAP Weldwood Contact Cement (not the automotive variety but checking the temp requirements it ought to hold- may regret that later but didn't want/need a gallon of the auto version) I started at the thick horizontal line where the trim pieces sit and applied a line only as thin as the embossed piece all the way across. Double checked that I had everything lined up and pressed the vinyl over the board, using the flat edge of the plastic squeegee that had come with the graphics kit to apply pressure and get it into place.
You may need a heat gun or hair dryer to soften up the vinyl a bit if there are wrinkles it needs stretched. Used a heat gun on mine and as long as you're patient and measure twice, glue once, the process is simple.
Picked the thick line as I wanted to use it as an anchor for applying the rest.
Once that had dried for 30 minutes or so I moved down the panel to the next thin line, let it dry then moved on. The most tedious point was the vertical pieces in the center of the panel. I used a thin foam brush to apply the cement, if you get it over the line it will show up after it's together if you don't wipe it off. Acetone works though don't let it sit on the vinyl.
After the front was all in place went around the edges with the cement, double checking everything lined up and the vinyl made it over all the corners.
The corners and front top curved area had been stapled from the factory. I was unable to find anything short enough that wouldn't pop clear through the panel & vinyl so took some 5/16" staples i had, taped them together then cut them as short as possible with tin snips before loading back in the staple gun. Took a few minutes but wanted to make sure the vinyl stayed on and I didn't ruin the whole thing by shooting holes in it.
By sheer coincidence I finished up the cementing process 46 years to the day after they had originally been done!
Here's the finished product, used SEM Vinyl Prep (about 3 servings of it to make sure it was as clean as could be), then adhesion promoter and finished off the panels with SEM Landau Black. Took just about 1 full can to do all four panels, I bought 3 extra so if any of you local guys need any let me know!
I think they turned out pretty nice and saved a bundle versus buying the repros!
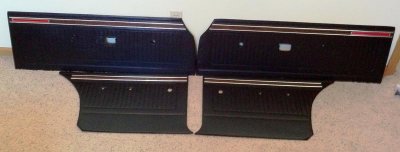