dpstark2
Well-Known Member
All,
Fellow B-Body-Board member Meep-meep and I set up this Sure Grip rear for my Charger a while back. The bearings, gears, etc., were all purchased from a reputable source we've all heard of that will remain nameless for now. The gears are US Gear (Strange). The pinion gear had a strange lip on it where the outer bearing shims rest that caused the shims to crush and would not allow us to achieve preload. The same supplier set us up with larger ID shims to solve this issue, which eventually got us a good preload.
No matter what we did, we could not achieve a good pattern on these gears. I made a check bearing and we settled on .086" on the inner bearing. This put the drive side pattern solidly on the tooth, but the coast side was somewhat lacking... More or less shim and one side would begin to walk of the tooth. After giving up, I put the unit in the car and tried it for a couple miles. It makes no noise in the air, but under load, it whines a bit at cruise and makes a lot of noise under decel. Backlash was set at .007", which may be a bit tight but helped center the pattern from root to tip.
Here are pics of the pattern on two different locations:
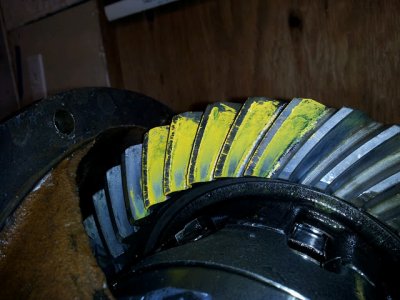
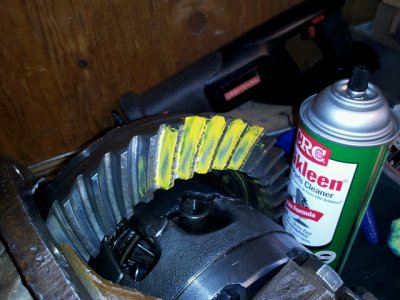
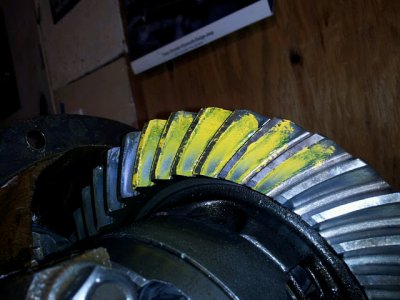
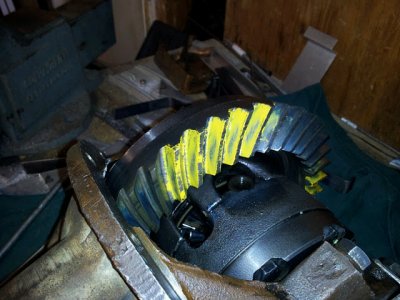
The supplier has simply said "they are set up wrong." From the very first issue with the pinion, I thought something was wrong with these gears. We even tried another case. I checked run out on the Sure Grip and found it at .002-3", which seems OK to me.
I know this has been covered, but does anyone have a specific comment based on the pictures? Are these gear just bad? Any help?
Fellow B-Body-Board member Meep-meep and I set up this Sure Grip rear for my Charger a while back. The bearings, gears, etc., were all purchased from a reputable source we've all heard of that will remain nameless for now. The gears are US Gear (Strange). The pinion gear had a strange lip on it where the outer bearing shims rest that caused the shims to crush and would not allow us to achieve preload. The same supplier set us up with larger ID shims to solve this issue, which eventually got us a good preload.
No matter what we did, we could not achieve a good pattern on these gears. I made a check bearing and we settled on .086" on the inner bearing. This put the drive side pattern solidly on the tooth, but the coast side was somewhat lacking... More or less shim and one side would begin to walk of the tooth. After giving up, I put the unit in the car and tried it for a couple miles. It makes no noise in the air, but under load, it whines a bit at cruise and makes a lot of noise under decel. Backlash was set at .007", which may be a bit tight but helped center the pattern from root to tip.
Here are pics of the pattern on two different locations:
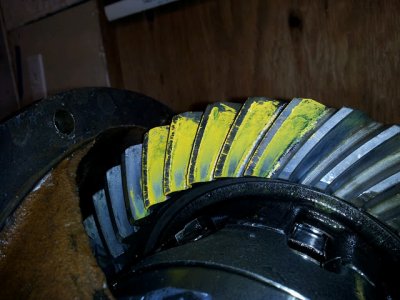
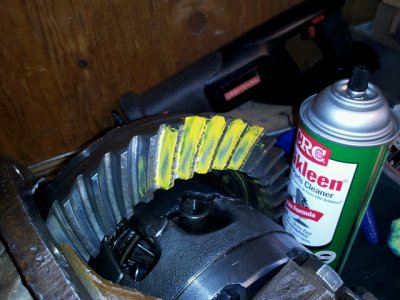
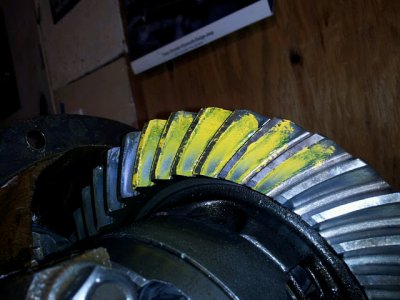
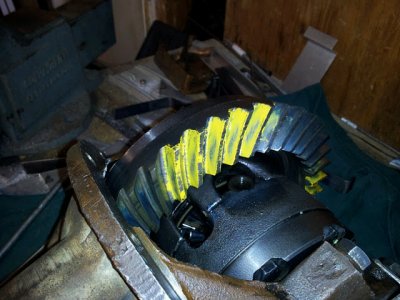
The supplier has simply said "they are set up wrong." From the very first issue with the pinion, I thought something was wrong with these gears. We even tried another case. I checked run out on the Sure Grip and found it at .002-3", which seems OK to me.
I know this has been covered, but does anyone have a specific comment based on the pictures? Are these gear just bad? Any help?