7t500
Well-Known Member
400-470, built in 2019. Less than 1000 miles on it. Sonic check results in attached picture. Only a mild ~500ish hp build with ~10:1 compression.
I found water in my oil and after taking the heads off I found a cracked cylinder wall on cylinder 1. I took the engine out and found another crack on cylinder 4.
Now it needs at least 2 sleeves and after looking at the sonic check results closer a few other cylinders have me nervous... what would you do? Spend the time and money finding a new block or spend the money on sleeves and run it?
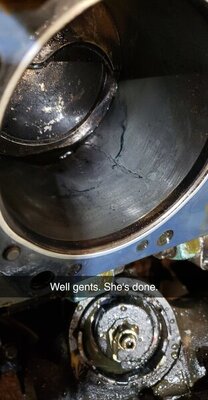
I found water in my oil and after taking the heads off I found a cracked cylinder wall on cylinder 1. I took the engine out and found another crack on cylinder 4.
Now it needs at least 2 sleeves and after looking at the sonic check results closer a few other cylinders have me nervous... what would you do? Spend the time and money finding a new block or spend the money on sleeves and run it?
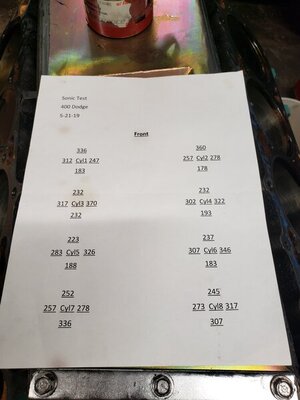
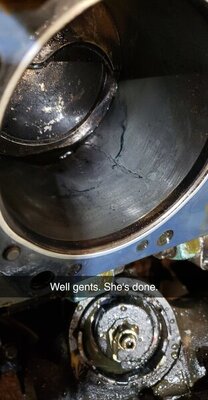