Update
Thanks for all the advice - lots of good stuff here.
I made myself a test weld out a piece of flat steel. I am not sure of the gauge, but I think it is 18 gauge (measured about 0.050"). I cut a section off and then drilled 5/16th holes in that. I also cut two long cuts in the remaining piece so I can butt weld and plug weld some.
I then checked many of the items that were suggested before I started welding again. I increased my heat range by one notch and decreased my wire feed a little bit. But the Aha moment came when I checked my wire. I have flux core 0.035" wire on the spool. Previously, I did not use gas. So now I need to buy a spool of the proper wire.
Then I will try again. I wish I had more hours to devote to this, but it is what it is...
Thanks for the continued help and encouragement! I will check back in once I get the proper wire and weld a little bit!
My test piece:
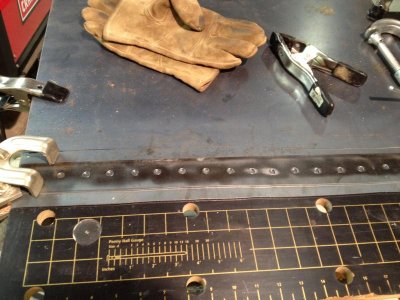
Thanks for all the advice - lots of good stuff here.
I made myself a test weld out a piece of flat steel. I am not sure of the gauge, but I think it is 18 gauge (measured about 0.050"). I cut a section off and then drilled 5/16th holes in that. I also cut two long cuts in the remaining piece so I can butt weld and plug weld some.
I then checked many of the items that were suggested before I started welding again. I increased my heat range by one notch and decreased my wire feed a little bit. But the Aha moment came when I checked my wire. I have flux core 0.035" wire on the spool. Previously, I did not use gas. So now I need to buy a spool of the proper wire.
Then I will try again. I wish I had more hours to devote to this, but it is what it is...
Thanks for the continued help and encouragement! I will check back in once I get the proper wire and weld a little bit!
My test piece:
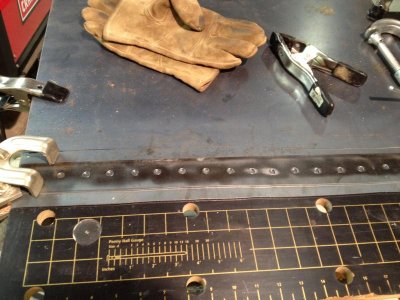