I am curious about the spot welder you have. Can you tell me about it?
I have wanted to get one but am a bit cautious about "learning how to use it" vs. the tried and true plug weld.
Don,
I have a Miller spot welder. It's a 220 Volt unit and I opted to pay a little more to get the one with a timer so I could make consistent welds. I had the blue cart left over from another old welder that I no longer have. I also purchased several different types of tongs to use in different locations on the car. These tongs are available in many configurations.
Initially I bought one from "China Freight". Never again will I buy anything from them.................... I had used it to weld in the new front radiator opening since I was upgrading from a 22 inch radiator to a 26 inch one................ I made about 15 - 20 spot welds with it and it quit working !!!!!! I tried to take it back, but since I didn't use it right away after I bought it, the warranty expired before I ever used it. It didn't matter that the thing crapped out on me only after using it once................ Don't waste your money there......................
Its really pretty simple to use since the spot welder has a timer on it. The timer goes from .01 seconds all the way to 5 seconds. The longer the length of time you set on the timer, the longer the current goes through the tongs creating the weld. I made a few metal coupons out of the same thickness sheet metal as my replacement panels, to try the spot welder out on before I used it on the car. While making some practice runs, I adjusted the timer until I got a good penetration. (I'm almost afraid that I may have the timer set just a little too long, and will back it off a fraction of a second). Then I tried to pry apart the spot welds from my experiment, and the actual metal ripped around the area that was spot welded. The welds themselves never broke loose.
As long as the metal is clean, and free of paint, all you have to do is close the tongs together and hit the switch to energize the unit. The timer does the rest and ensures that all welds are the same. The only down side is the actual unit that does the welding with the tongs is pretty heavy. It gets awkward at times. Another thing to watch out for is the metal you are welding together has to be making good contact with each other. If not, this will blow a hole through it, just like a torch would.
Overall it's very simple to use. It's quick and easy. Once your parts are spot welded together, your pretty much done. I do normally go back and grind off any excess flash spurs from around the spot weld, since these things are like razors and will slice the hell out of your finger tips later on when you are sanding on the car........... Ask me how I know this..............
Here's a few pictures of the spot welder I have. So far it has worked great (knock on wood). So far I have used it to rebuild a 1953 Chevy Truck Cab and sides of the bed for a friend of mine, plus the work I have done here on the Challenger. I wish I would have used one of these years ago. It's so simple and easy to use. Much easier in my opinion than plug welding with a MIG.
Hope this helps Don. Take care bud.................
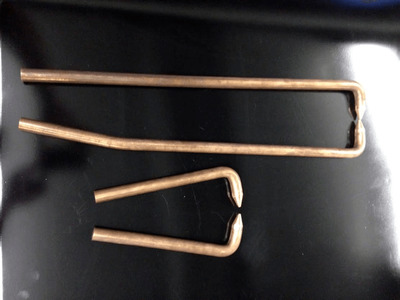