I left the weekend before with the clutch pedal sitting way too proud, a consequence of the female threaded adjuster shaft not threaded deep enough to completely screw it into the m/c pushrod. The m/c cylinder had to come back out anyway because the shifter tang on the steering column was in the way of the m/c hydraulic lines.
Before removing the m/c, I marked the pushrod where the shaft ended (with the jam nut spun down out of the way). I removed the shaft from the pedal, unscrewed the shaft, then reattached the shaft to the pedal, letting it hang down. Pushing the pedal down to brake pedal height while holding the shaft next to the pushrod, I made another mark on the pushrod. The length between the two marks was how much had to be cut off the top of the pushrod.
Holding the m/c secure with the jam nut, off came the top. The yellow mark is the original depth of the shaft, the other mark is hidden by the jam nut.
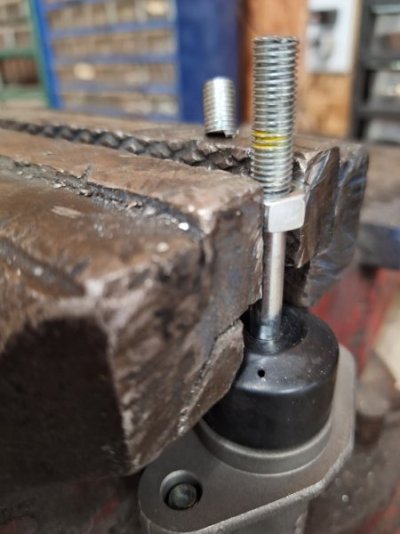
I forgot to take pictures of the new pedal placement, more to come later.
Before removing the m/c, I marked the pushrod where the shaft ended (with the jam nut spun down out of the way). I removed the shaft from the pedal, unscrewed the shaft, then reattached the shaft to the pedal, letting it hang down. Pushing the pedal down to brake pedal height while holding the shaft next to the pushrod, I made another mark on the pushrod. The length between the two marks was how much had to be cut off the top of the pushrod.
Holding the m/c secure with the jam nut, off came the top. The yellow mark is the original depth of the shaft, the other mark is hidden by the jam nut.
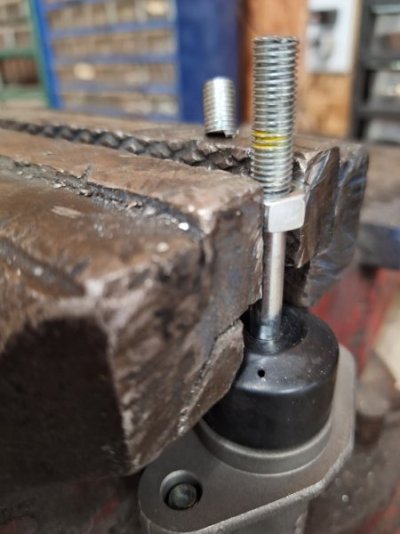
I forgot to take pictures of the new pedal placement, more to come later.
Last edited: