- Local time
- 10:00 PM
- Joined
- Oct 16, 2014
- Messages
- 29,607
- Reaction score
- 73,202
- Location
- Salisbury, Vermont
Cut a paddle/ handle out of 3/16 plate steel. Marked the plate to cut out the slot it will set in. Drilled both ends. Will cut the slot in the morning. The plate with the slot will be about 1 1/8" wide and about 1/4" longer than the handle on each end. This resulting meat will give it rigidity and provide an edge to weld it to the door panel. Spacing is key so it ends up flush and not above or below the panel. I left the gap between handle and slot very small so the thing disappears into the paint job. I'm mounting it on top of the door in the valley along the window slot. When the handle comes up on a pinned fulcrum the wider end swivels down. That portion where it would be the outline of the thumb button gets a ball from the stock mechanism that the end of the rod clips onto. If the rod ends up too short i'll either make a longer one or put a adjustable sleeve in it. So, easy peasy. lol. And slick. All you will see is a 3/16" flat bar in it's slot once done and painted. The tail end of the 3/16" bar gets a small divit about 1/8" in from the end. That's for the small push rod that will be on my keyring. Just set the end of the rod in the divot and push down and the other end comes up to grab and lift to unlock the door. A return spring will go hanging from under the handle near the rear tab..I'll hammer and dolly the original holes and weld in new metal leaving them smoothed over. Power locks so that goes too..
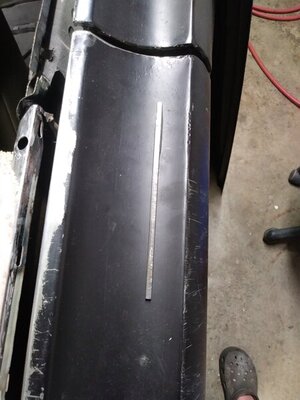

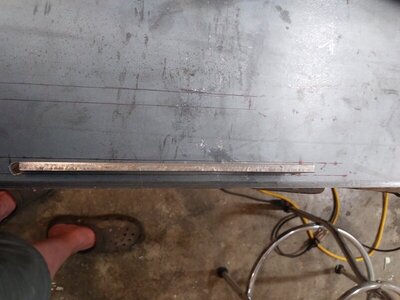
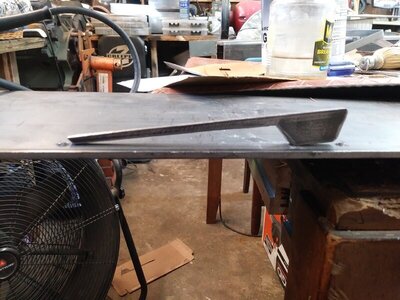
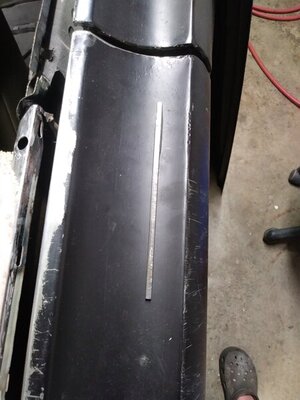