QQ1 68 GTX
New Member
NICE work! I have the same color coded GTX. It’s going to be rotisseried next month. My father bought it in 1982 for $750 and drove it home. I had it painted but got screwed so decided to have it done correctly. QQ1 with light blue door frames and headliner. Same color dash as yours also. Mine is factory console 4 speed, power disc brakes, tach, black vinyl top, white side stripes & performance paint on the hood.
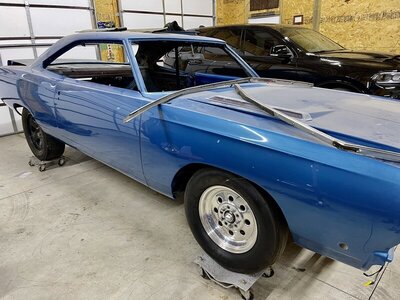
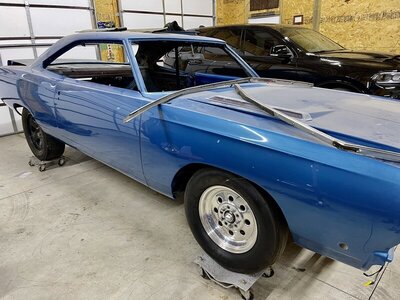