Just a couple things to consider...
First would be using a 'good' set of tappets, so no excessive bleed-down. That would creat a gap from part to part.
The overall build of the motor, meaning cutting the heads or block, how much it was cut, and the thickness of the head gasket used. Keep in mind the head surface to crank centerline is a given measurement. If changed, adjustments must be made to get correct clearances.
If your sure the motor is 'stock', with no major changes to the head surface to crank centerline, the valvetrain should fall into place, assuming the right parts are used.
Use cylinder #1, for example, at TDC compression stroke. That would put both #1 tappets on the base circle of the cam. There should NOT be any up and down play for the two pushrods. You should be able to easily spin the pushrods, that show there's no excessive pressure. Of course, you've got to remember tappets work off of oil pressure, but even without, there should not be play at the pushrods.
Can't find it right now, but...correctly set up, when the tappet is sitting on the cam's base circle, the plunger in the tappet should be pushed down, via the pushrod, a minimum of .010"...max .050. That measurement is from the top of the plunger to the retainer clip, or wire.
That makes a zero 'lash' at the rocker arms...no up and down play.
If you do have play, 'something' is wrong.
- - - Updated - - -
Here's a one size fits all for hydraulic tappets.
This one shows .020 to .060.
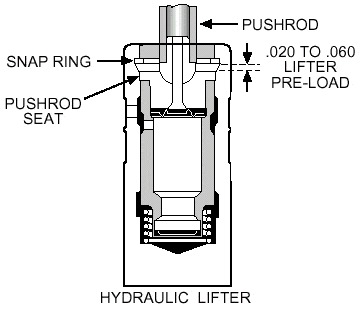