Mini tub in convertible - design time . . .
Part of the rebirth is going to be part design and rebuild . . . Mini Tubs ! ! !
I really want to mini-tub this bad boy, to allow me to be able to put the larger tires/wheels and give me that deep dish look that I love so much. So I've shot a bunch of pictures and drawn out some lines . . . and I've got some questions for the group . . .
Here's what we're working with here . . . on the top we have 2 3/4 inches to the inner wheel well lip ( this is at the top of the wheel well ).
My concern - it the to flange of the frame that is sticking out to the 11/16 mark on the tape.
If I cut this off, am I hurting the strength of the frame torque-box structure ? I know that it'll be re-welded - but is that as good ( or better ) ?
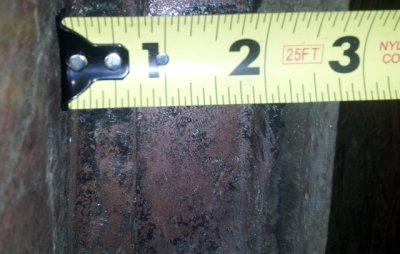
Now if we move down to the bottom of the wheel well ( just under the seat belt bolt connection ).
Now we're running 3 1/4 inches . . . a 1/2 inch more . . . so now I have to make a 1/2 inch gap ? ?
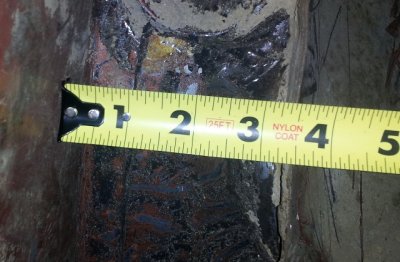
Inside the car we'll have to move this inside of the well to the right 2 3/4 inches - I've got room.
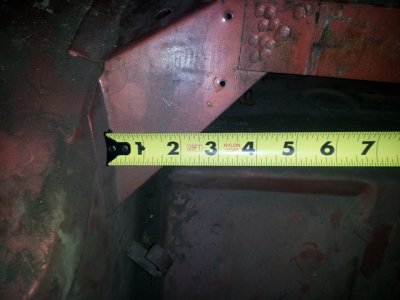
And I need to move the bottom here either 2 3/4 inches or 3 1/4 inches . . . that what I'm trying to figure out.
Not - I'm going to loose one of my seat belt connections with the cut - so it'll have to be re-located.
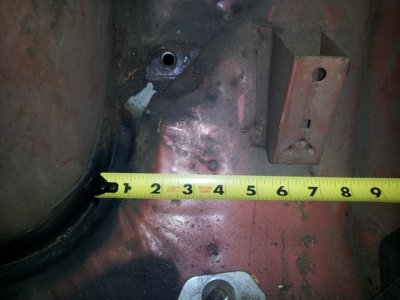
Drew out some lines for the proposed cuts in the cab area of the car . . .
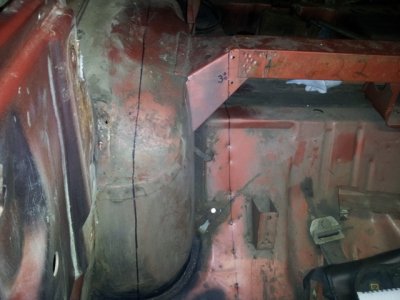
And in the trunk area of the car . . . notice that I've got a little swiss cheese in the trunk that'll need to be cleaned up.
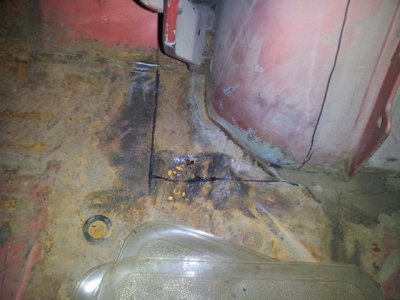
This is another part of this mini tub project, moving the spring perches to allow pulling the perches in 3" inches.
What you can see is that the original mounting position is much higher than the new on - the frame hangs much lower . . .
so does the mounting hole go at the same lever - and if it does, will the shackles still hold the springs correctly ?
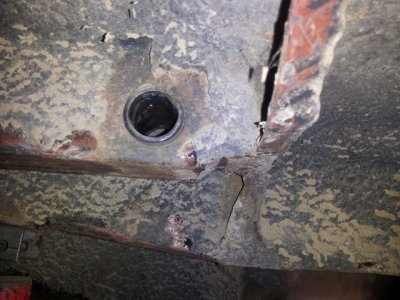
Stumbled on this in the process, had not seen it before. Apparently during the build process, somebody wrote the date on this panel inside the cab area of the car. If you look you can see 6-22 on the panel - my guess is that is the approximate date that the car was built during 1967. Pretty cool ! ! !
Might have to re-shoot the picture to remove the glare.
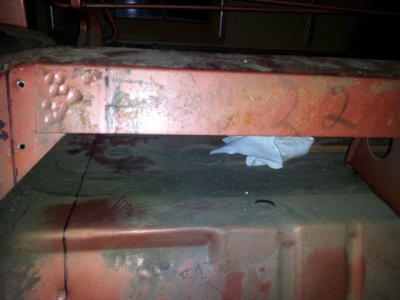
So . . . now to figure out how to get this cut out and re-welded back in to give mt tires/wheels some much needed room !
Here's a little diagram to try and illustrate the (2) options:
Part of the rebirth is going to be part design and rebuild . . . Mini Tubs ! ! !
I really want to mini-tub this bad boy, to allow me to be able to put the larger tires/wheels and give me that deep dish look that I love so much. So I've shot a bunch of pictures and drawn out some lines . . . and I've got some questions for the group . . .
Here's what we're working with here . . . on the top we have 2 3/4 inches to the inner wheel well lip ( this is at the top of the wheel well ).
My concern - it the to flange of the frame that is sticking out to the 11/16 mark on the tape.
If I cut this off, am I hurting the strength of the frame torque-box structure ? I know that it'll be re-welded - but is that as good ( or better ) ?
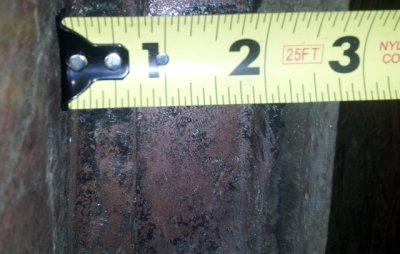
Now if we move down to the bottom of the wheel well ( just under the seat belt bolt connection ).
Now we're running 3 1/4 inches . . . a 1/2 inch more . . . so now I have to make a 1/2 inch gap ? ?
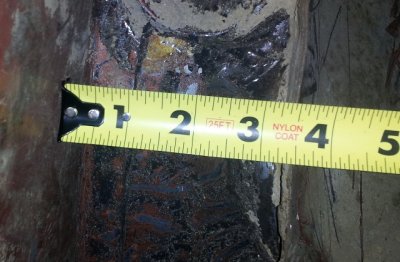
Inside the car we'll have to move this inside of the well to the right 2 3/4 inches - I've got room.
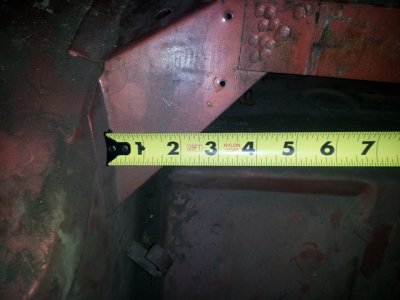
And I need to move the bottom here either 2 3/4 inches or 3 1/4 inches . . . that what I'm trying to figure out.
Not - I'm going to loose one of my seat belt connections with the cut - so it'll have to be re-located.
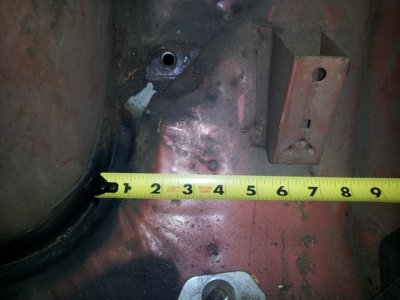
Drew out some lines for the proposed cuts in the cab area of the car . . .
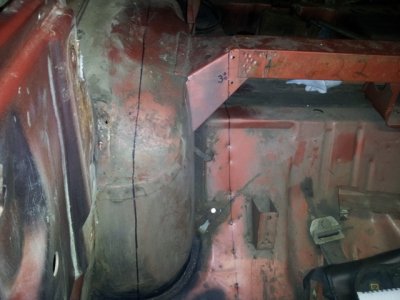
And in the trunk area of the car . . . notice that I've got a little swiss cheese in the trunk that'll need to be cleaned up.
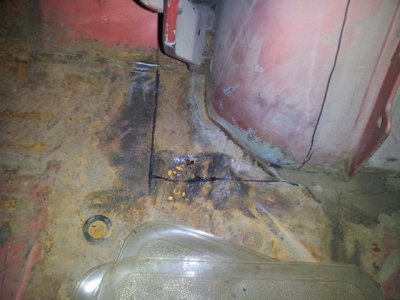
This is another part of this mini tub project, moving the spring perches to allow pulling the perches in 3" inches.
What you can see is that the original mounting position is much higher than the new on - the frame hangs much lower . . .
so does the mounting hole go at the same lever - and if it does, will the shackles still hold the springs correctly ?
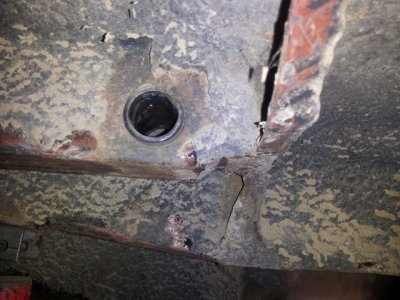
Stumbled on this in the process, had not seen it before. Apparently during the build process, somebody wrote the date on this panel inside the cab area of the car. If you look you can see 6-22 on the panel - my guess is that is the approximate date that the car was built during 1967. Pretty cool ! ! !
Might have to re-shoot the picture to remove the glare.
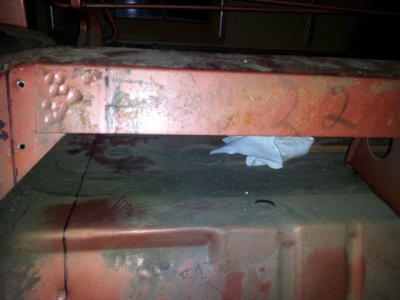
So . . . now to figure out how to get this cut out and re-welded back in to give mt tires/wheels some much needed room !
Here's a little diagram to try and illustrate the (2) options: