Hey fellas,
I spent hours working on the Fury this weekend and made some excellent progress, though not without some difficulties.
In my previous couple of posts you see the doors and fenders in place, but the fenders weren't really attached to much of anything; they were bolted at the door jams but the forward ends were resting on shims; what I really needed was to get the rad support in place so the fenders have a permanant, fixed point to bolt on to.
Since I still have the bumper filler panel and the hood latch support, both of which bolt between the fenders, I used these two pieces to set the fixed distance the fenders, then centered them on the chassis.
This picture shows various pieces of string strung between the frame rails and the center points marked. Another piece of string was pulled (at 90 degrees to the other strings), running along the center points towards the front of the car. This string allowed me to accurately find the center point of the bumper filler panel.
From there I had to set the fender height so I used my digital level sitting on top of a straight edge running between the fenders.
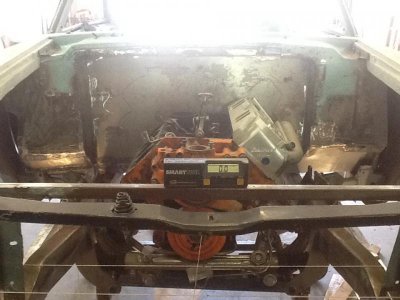
But now is when the trouble began. I now had the fenders in place, level, and pretty much where they'd be at final assembly, so I decided to take some measurements at common points on both fenders, like the pointed tip and wheel arch.
Here are pictures of the measurements taken at the tips of the fenders; you'll notice the measurements are not the same.
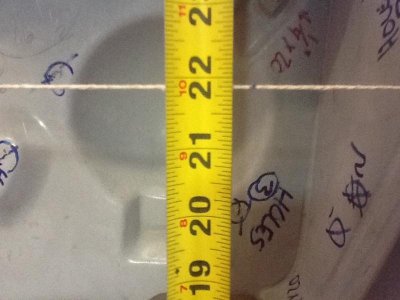
Wondering WTF I had done I used my digital level and checked the string running between the tips; I was within .1 degree.
Totally confounded I moved on to measuring the wheel arches:
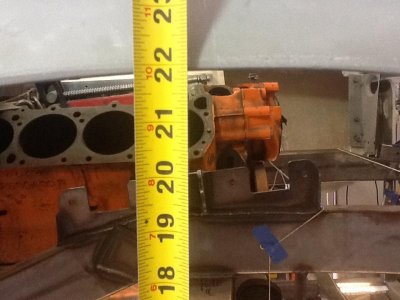
For the life of me I couldn't figure out what I'd done to knock the fenders out of alignment so I put my straight edge back across the fenders, and guess what; they were still level!
I spent the rest of Saturday trying to figure it out and the only thing I can come up with are errors creeping in during the manufacture of the fenders. The fenders are an assembly of smaller pieces bonded together and if errors begin to creep in the fenders won't be symmetrical.
I decided the best course to follow would be to use my established centerline and level lines and build the rad support around those known measurements.