mopar4don
Well-Known Member
A-pillars are DONE!
Did a little patch on the drivers side
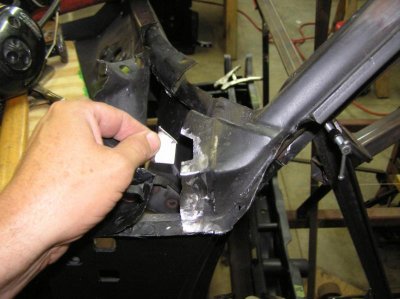
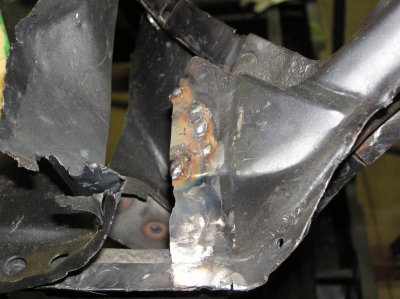
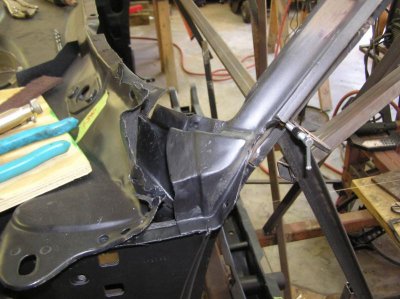
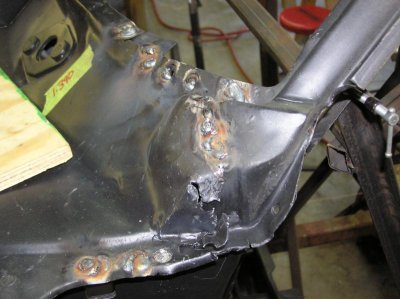
I had a LOT of trouble getting these seams to blend out using disk grinders.
Ended up using a file. the problem is it takes a LONG LONG time to file down welds, and get it good.
But thats what I did and this is what how it looks. (NO FILLER by the way)
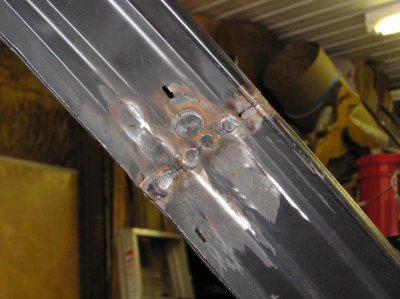
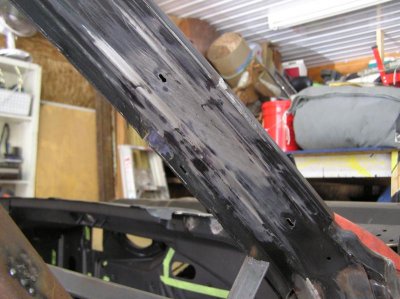
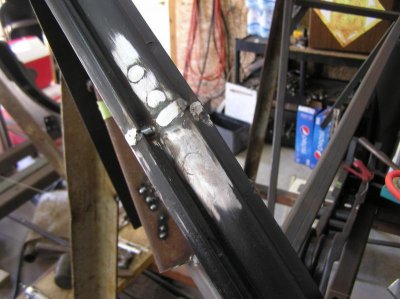
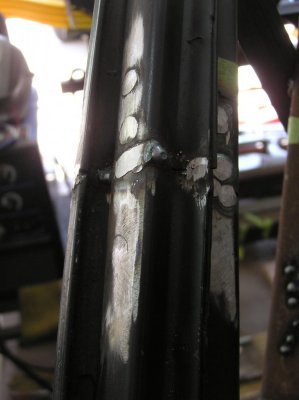
Used the sharpie as a guide coat
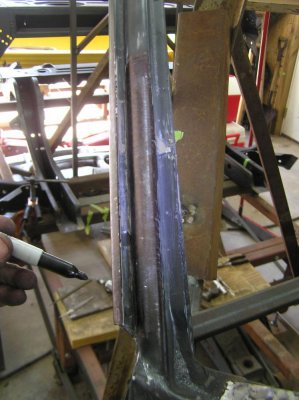
then
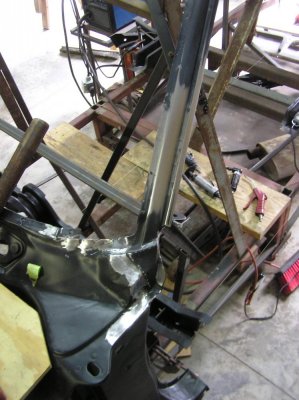
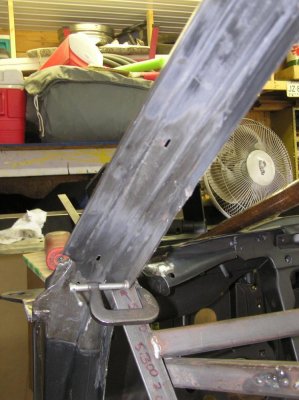
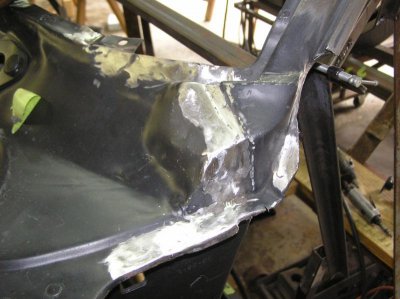
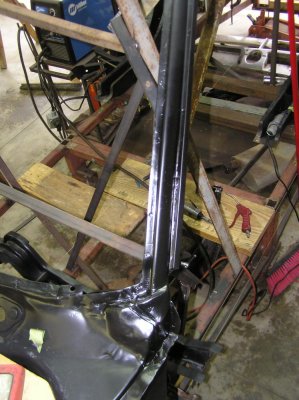
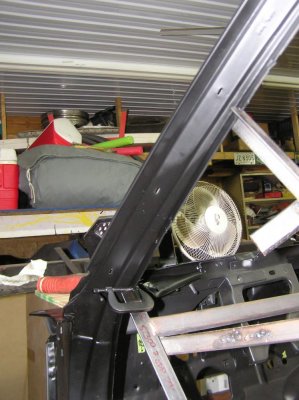
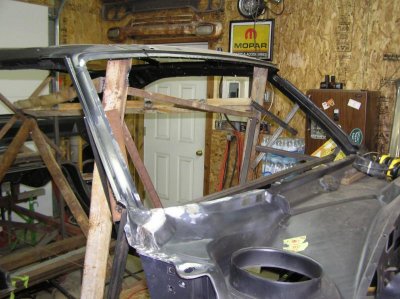
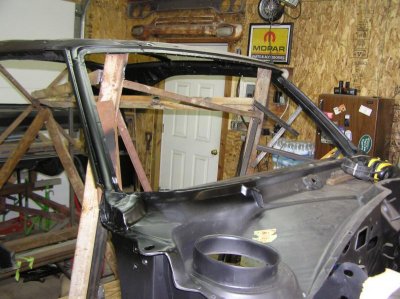
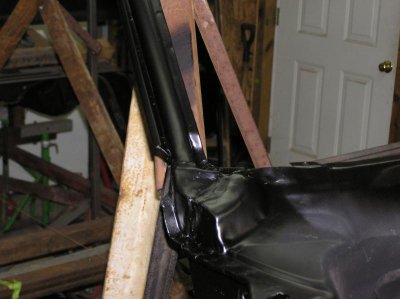
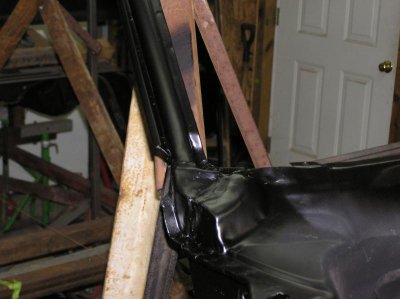
Did a little patch on the drivers side
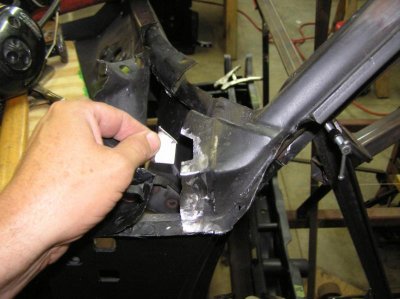
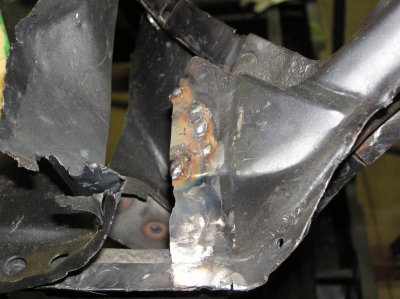
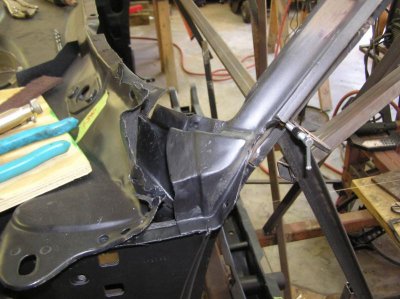
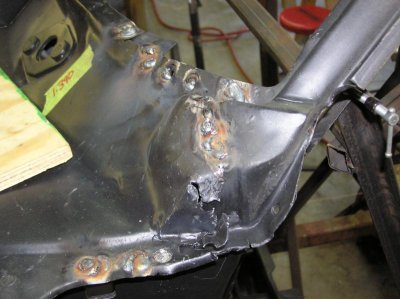
I had a LOT of trouble getting these seams to blend out using disk grinders.
Ended up using a file. the problem is it takes a LONG LONG time to file down welds, and get it good.
But thats what I did and this is what how it looks. (NO FILLER by the way)
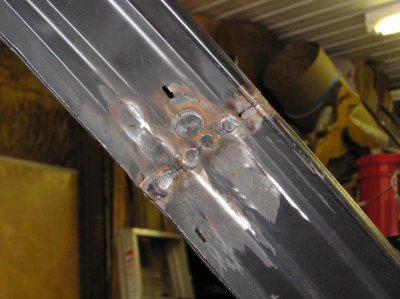
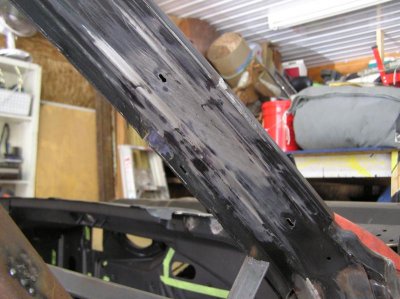
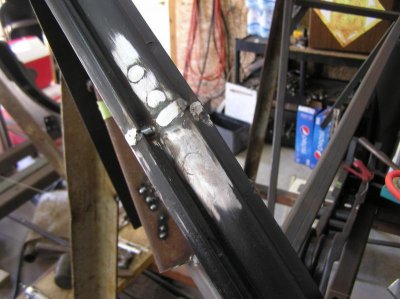
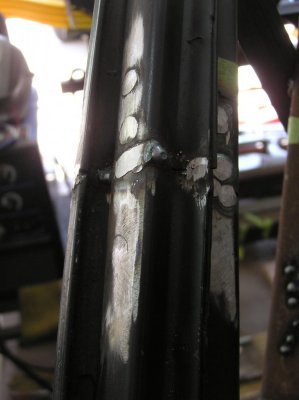
Used the sharpie as a guide coat
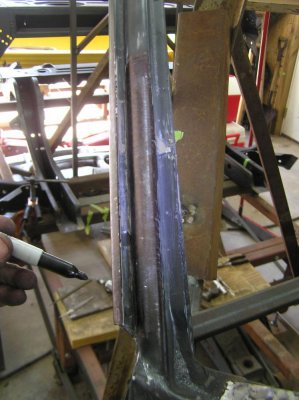
then
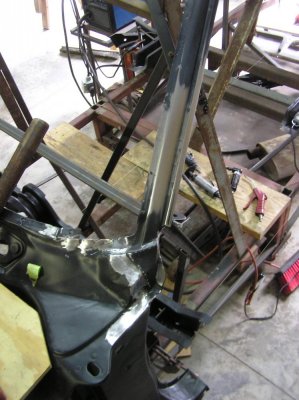
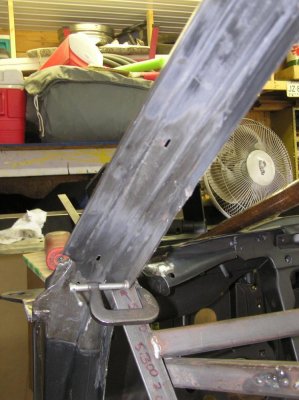
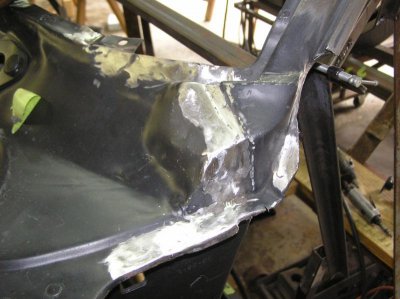
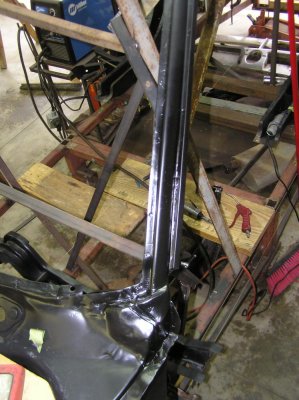
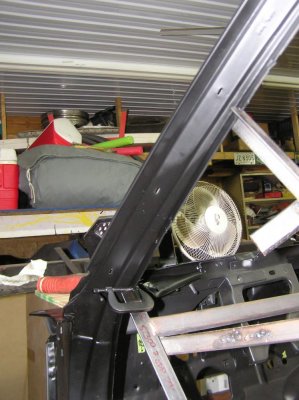
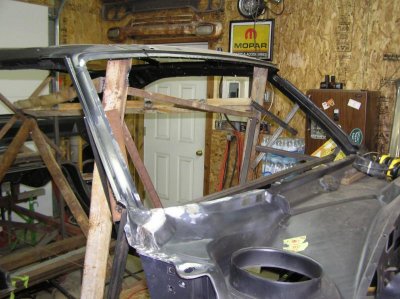
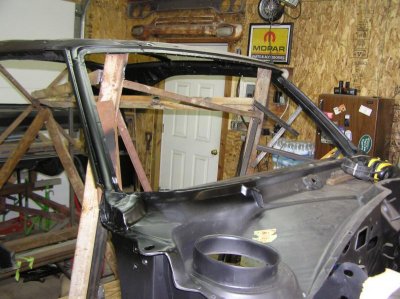
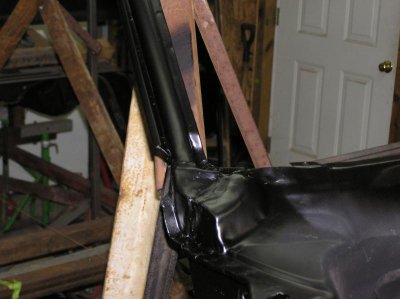
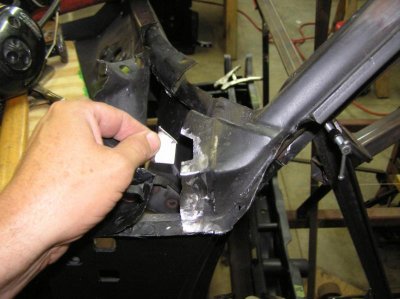
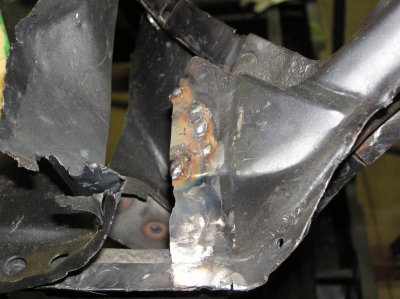
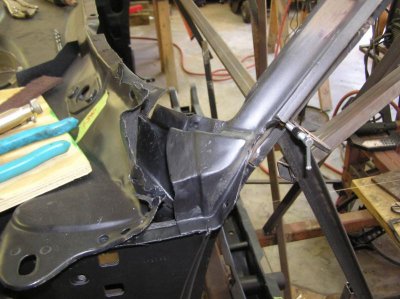
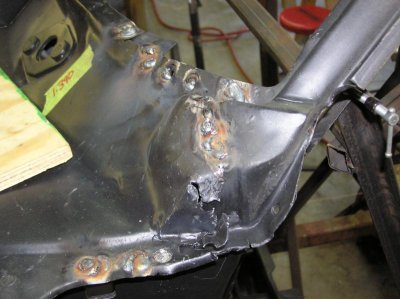
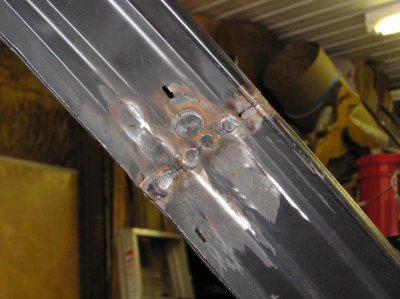
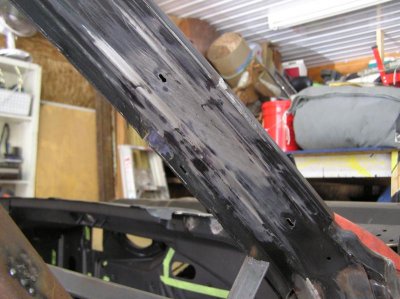
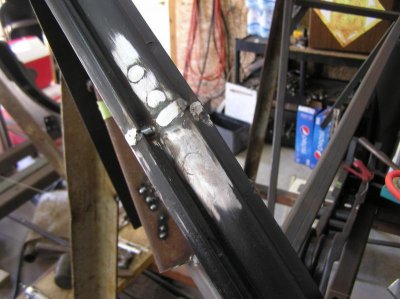
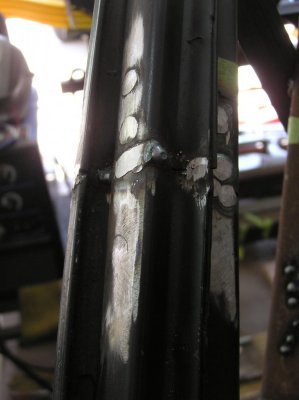
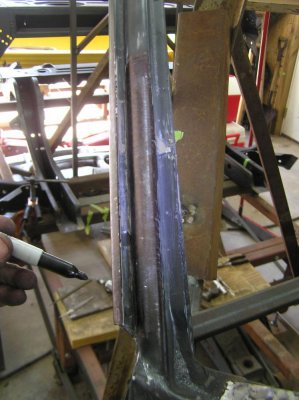
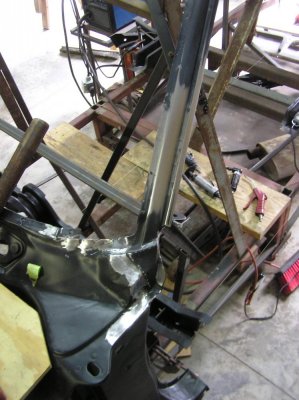
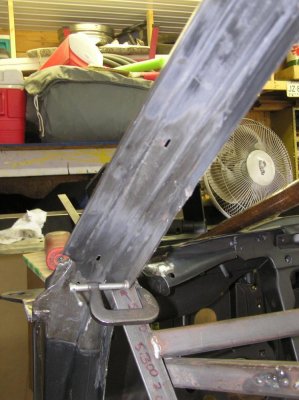
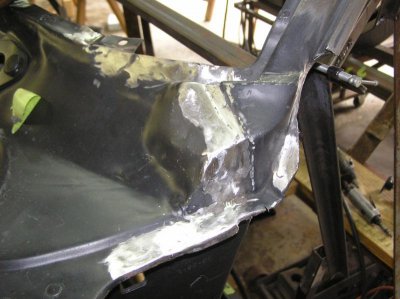
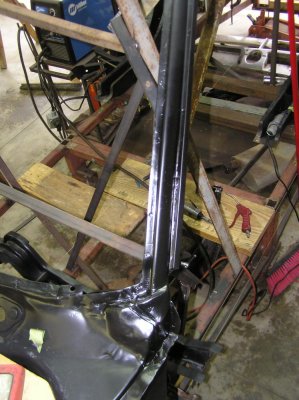
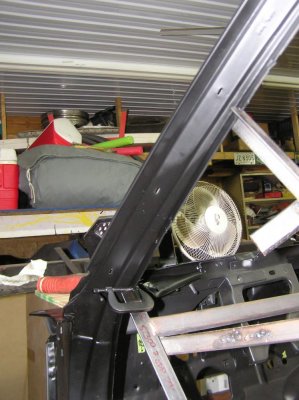
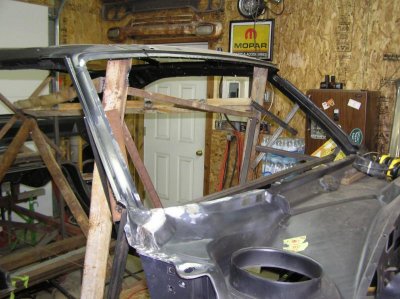
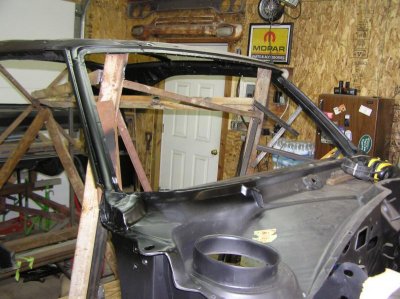
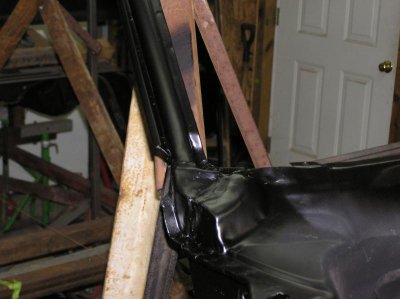