Glenwood
Well-Known Member
- Local time
- 8:18 AM
- Joined
- Jun 19, 2015
- Messages
- 2,929
- Reaction score
- 2,854
- Location
- Kawartha Lakes, Ontario
took in the local car show yesterday. Not may mopars unfortunately but this one caught my eye! Same owner since new...beautiful
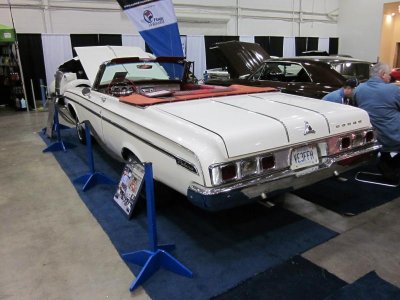
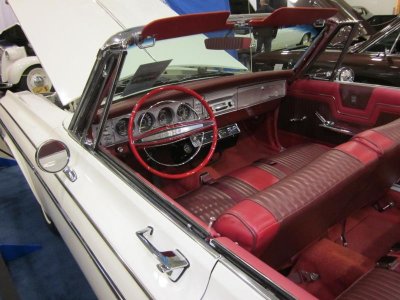
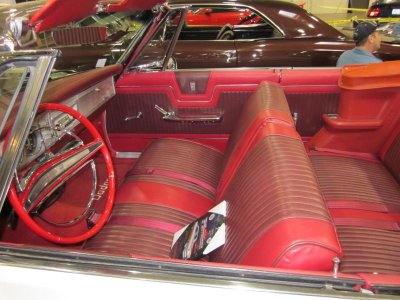
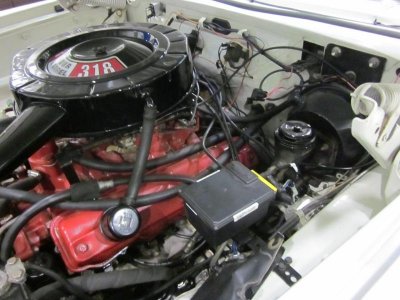
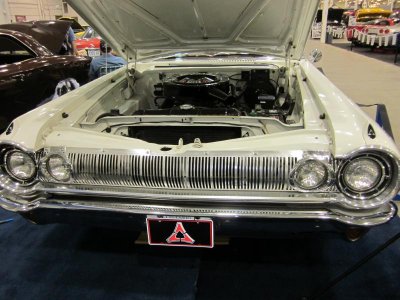
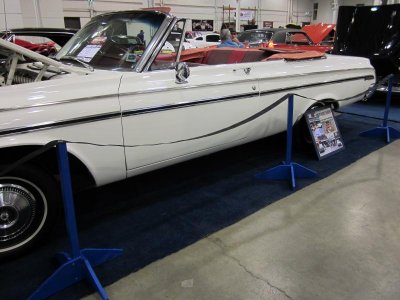
- - - Updated - - -
finished welding up these patches today
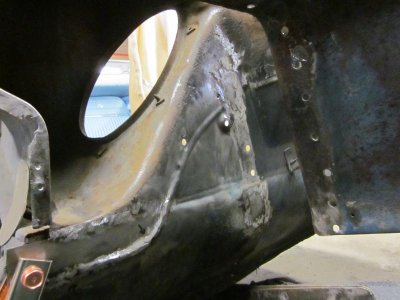
- - - Updated - - -
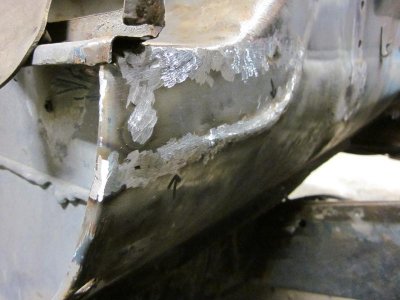
- - - Updated - - -
found a few more rust pin holes. Probably should have cut and patched but I managed to fill them in.
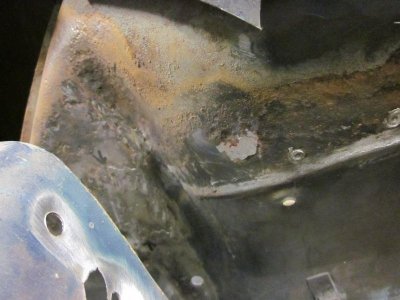
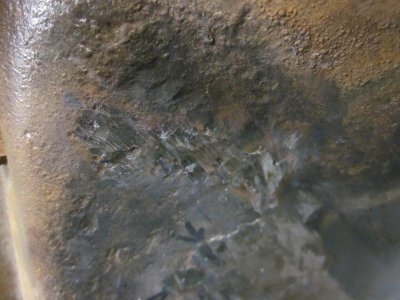
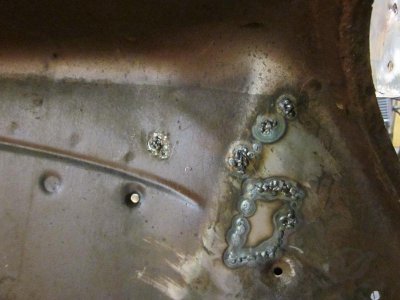
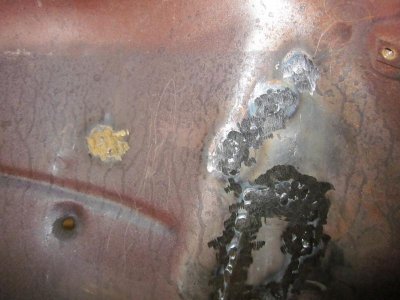
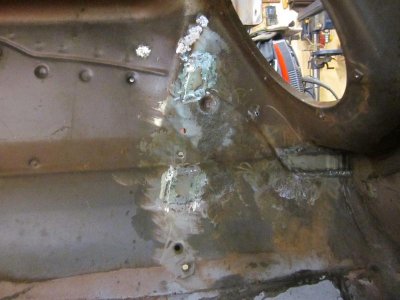
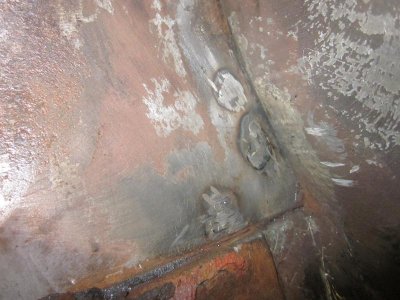
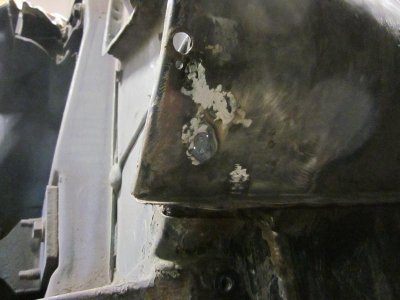
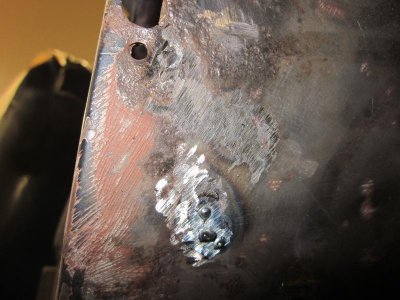
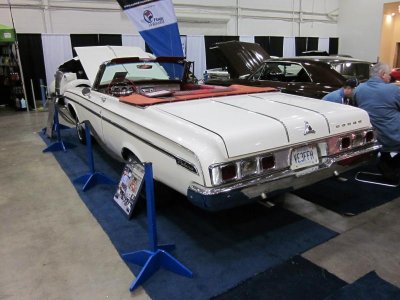
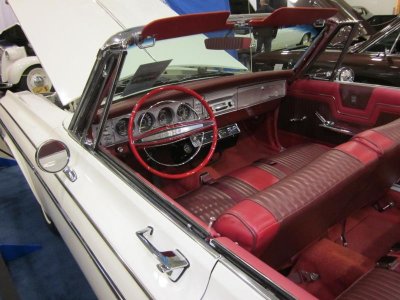
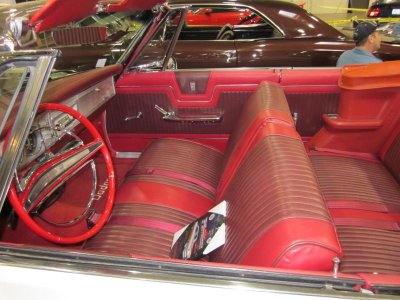
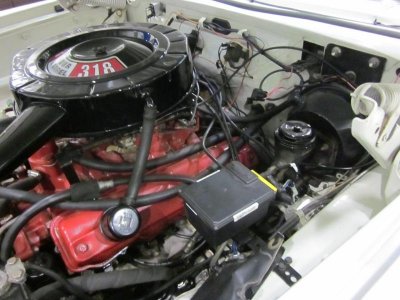
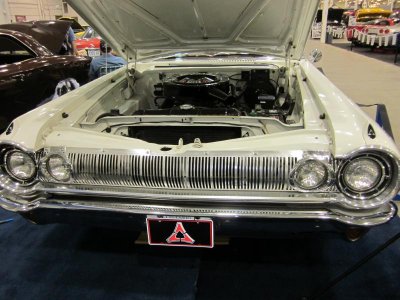
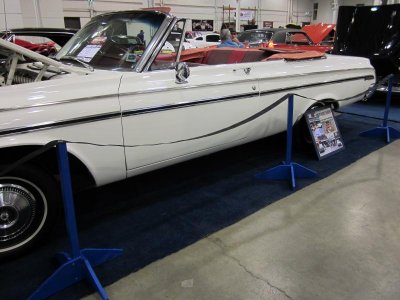
- - - Updated - - -
finished welding up these patches today
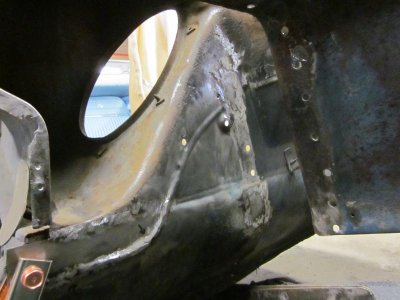
- - - Updated - - -
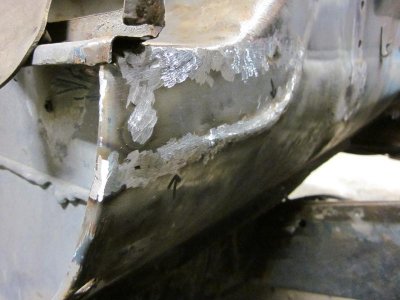
- - - Updated - - -
found a few more rust pin holes. Probably should have cut and patched but I managed to fill them in.
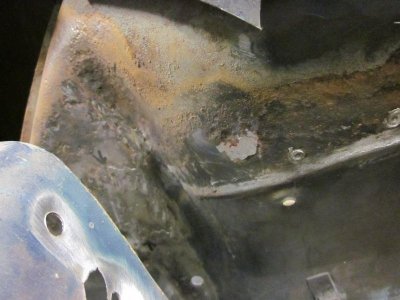
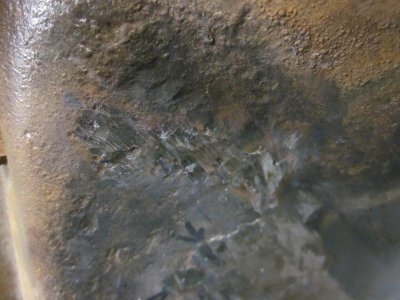
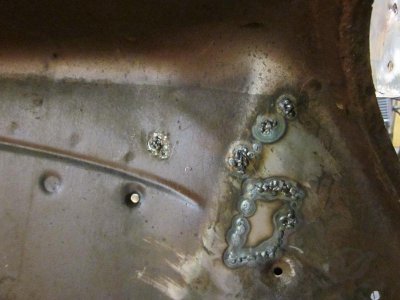
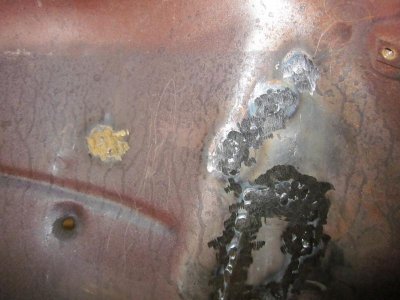
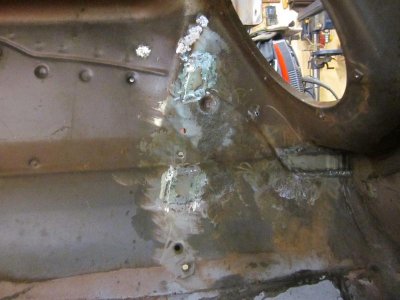
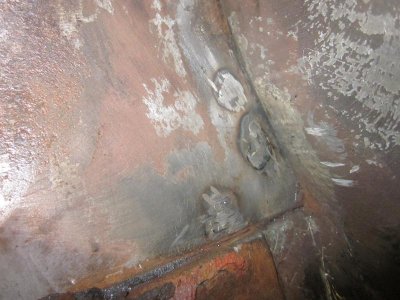
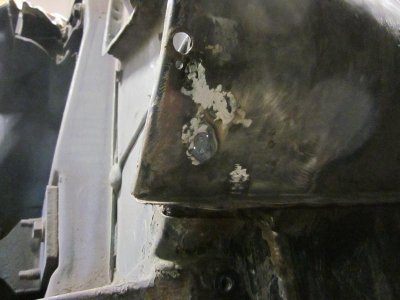
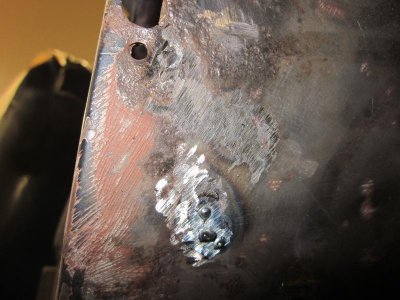